2000 - Volume #24, Issue #1, Page #20
[ Sample Stories From This Issue | List of All Stories In This Issue | Print this story
| Read this issue]
Blacklight Painting Systems "Extends Equipment Life By Years"
![]() |
![]() |
![]() |
If you follow Jim Deardorff's advice, paint jobs and the equipment they cover may last a lot longer, thanks to special materials and blacklight inspections. The Chillicothe, Missouri painter takes a lot of pride in his work. That's why it bothered him when he couldn't get paint to stick to fertilizer equipment and other machinery.
" I would sandblast and paint until I was blue in the face, but I couldn't get it to last," recalls Deardorff. "It took me years to discover that it was the soluble salts in the metal that were blowing the paint off."
Today, Deardorff's paint jobs are lasting years, even on tough soluble salt encrusted equipment like fertilizer spreaders. One fuel tank paint job has lasted 15 years with no sign of failure. They are lasting so well, in fact, that he sees no reason a properly prepared and maintained paint job shouldn't last 100 years. The secret, he says, is to eliminate stress on the coating, both internal stress from the metal and external stress from light and chemicals. Deardorff does this through a combination of rigorous cleaning and coatings he has developed.
The problem, he says, is that the paint industry has little interest in his techniques. The industry wants to sell more paint," explains Deardorff. "Why would they introduce a technology that would double the life of a paint job?"
Deardorff no longer waits for the paint and coating industry to accept his system, but practices what he preaches and preaches what he practices to anyone who listens. While he markets his system and supplies under the name Ultraviolet Responsive (UVR) Lifeservice Painting System, he says anyone can adapt elements of it to their own paint jobs and extend the effective lifetime of a coating significantly.
The process begins with a proper cleaning. For a complete repainting, he sandblasts twice to remove old paints and corrosive materials. Once the old finish is off, he applies a special aviation cleanser that reacts with salts and other corrosive agents still on the surface. It is those salts, he says, which if left in place will react with moisture seeping through cracks and pinholes in aged paint, forming acids that corrode the metal and blister the paint.
Deardorff has formulated the cleanser to the consistency of wax polish, and added a bonding agent that fluoresces blue on contact with a surface. After the cleanser has set, he goes over the project with a blacklight to find black spots which indicate more cleanser is needed to saturate to the surface. Once the surface has a uniform coat of cleanser on it he proceeds to a high pressure washing, a process that can take repeated passes to remove all signs of the fluorescent cleanser and the contaminates it has bound to. He reports that some materials can require up to 36,000 lbs. of water pressure to be washed free.
Another blacklight inspection reveals unremoved cleanser/contaminants requiring more water. Once the surface is free of fluorescent material, Deardorff applies a special clear primer containing an inorganic anti-corrosion material he obtains from a Swiss company. Again a fluorescent material is added.
"For corrosion to occur, there has to be oxygen present," he explains. "This material eliminates oxygen air pockets beneath the coating."
This time the blacklight inspection identifies any spots not covered with primer. Deardorff adjusts the amount of fluorescent material according to the thickness of the final paint job. Once the entire surface is covered with primer and no black spots can be found, high quality zinc based paint is applied until no fluorescing primer can be detected. Again blacklight inspections ensure complete coverage.
"Most paints have organic binders and UV light breaks down organic materials," says Deardorff. "Zinc isn't an organic binder."
Once
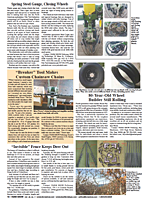
Click here to download page story appeared in.
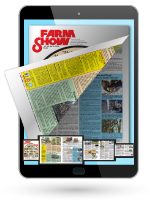
Click here to read entire issue
To read the rest of this story, download this issue below or click here to register with your account number.