2001 - Volume #25, Issue #4, Page #42
[ Sample Stories From This Issue | List of All Stories In This Issue | Print this story
| Read this issue]
Former Dairy Farmer Now Makes Manure Pumps, Repairs Mixers
![]() |
That's why, he says, after several years of dividing his time between dairy farming and selling silage and manure handling equipment, he decided to turn his empty dairy barn into a custom farm equipment fabrication shop.
He had started making manure pumps from new Browning transmissions when he was approached by Neal Koepke, an Edgar, Wis., dairy farmer, who wanted to know if he could make one from the gearbox on an old square baler. Koepke had heard a story about someone who had done it but he didn't know how.
Friedenfels agreed to give it a shot if Koepke would provide the parts.
Koepke located a Deere 14T baler at a dealership and paid $50 for it. Friedenfels tore the gearbox down and successfully modified it to pump manure.
"A new pump and motor were going to cost me $6,000 or so," Koepke says. "Including what I paid for the baler, Mike's pump was less than half that, and he installed it, too."
Word of the baler gearbox-turned-manure pump spread and Friedenfels' phone began ringing with requests from dairy farmers who wanted one.
"I invested in some shop tools and began making more and more of them," he says. "There are hundreds of old balers sitting around that nobody wants so we're recycling parts. After all, a manure pump is really just a gearbox with arms on it. We make use of the flywheel, too, because that allows the pump to work better with less power."
Friedenfels has made about 80 manure pumps since he built the first one for Koepke six years ago. "We've made several changes in the design over the years," he says. "Just about any baler transmission will work for these pumps."
With one full-time employee, he made and installed 20 pumps the year before last. He says last year was a little slower because of lower milk prices.
In the process of making and installing manure pumps, Friedenfels identified another need on many dairy farms. "Dairymen who feed total mixed rations needed someone to repair their TMR mixers," he says. "Half my business now is rebuilding mixers. We fabricate new parts, remanufacture augers and flighting, and basically restore them to near-new condition at a fraction of the cost of a new machine."
In the process of working on mixers he has come up with a number of his own repair methods.
"I can rebuild augers ranging in diameter from 4 in. to 3 ft.," he says.
He also fabricates manure handling augers and conveyors. "I've developed an auger that can be used with sand bedding," he says. "Not many augers can handle both manure and sand, but we've come up with the right materials, bearings and seals to do it."
Friedenfels says he's not spent a cent on advertising his business, yet he has more than enough to keep him busy. He says the secret to running a successful fabrication business is being able to help customers solve their problems with quality equipment and then providing the service to back it up. "That, and you have to be happy doing what you're doing," he says.
He figures the need for custom fabricating shops like his is on the increase, as farmers everywhere want equipment modified to fit their needs or just need things rebuilt to save the cost of buying new.
Contact: FARM SHOW Followup, Mike Friedenfels, Friedenfels Equipment, N1379 Oak Drive, Medford, Wis. 54451 (ph 715 678-2860).
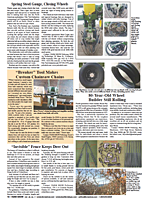
Click here to download page story appeared in.
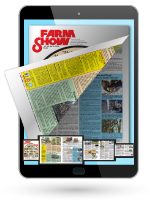
Click here to read entire issue
To read the rest of this story, download this issue below or click here to register with your account number.