1995 - Volume #19, Issue #2, Page #11
[ Sample Stories From This Issue | List of All Stories In This Issue | Print this story
| Read this issue]
Home-Built Shelled Corn Grinder
![]() |
"I use it to creep feed cracked corn to my 50 cows. It really works good," says Cates.
The grinder consists of a 3 by 2-ft. wooden box mounted on a pair of wheels, with a 1-bu. steel hopper inside. A pair of 8-in. long, 4 1/2-in. dia. steel rollers are positioned at the base of the hopper. One roller is belt-driven by a 1 1/2 hp electric motor while the other is stationary. As corn gravity feeds from the hopper, grooves in the top roller pull it in between the two rollers and crack it. Corn drops into the box and is unloaded out a chute on one end.
"It has paid for itself many times over. I even use it to custom grind corn," says Cates. "It cost about $400 to build. I can grind about 45 bu. per hour with it. Usually I grind about 100 bu. at a time. The position of the stationary roller can be adjusted to control the amount of grinding action on the kernels.
"The electric motor turns at 3,600 rpm's. I mounted a 2-in. dia. pulley on the
motor and a 6-in. dia. pulley on the top roller to reduce the rpm's to about 1,800. I
use a bucket to scoop corn into the hopper. "I've built three models so far. I built
my first one three years ago with 4-in. long rollers. I built another one for a friend with 10-in. long rollers for increased capacity." Contact: FARM SHOW Followup,
Dockery Cates, 5341 County Road 320, Enterprise, Miss. 39330 (ph 601 659-7744).
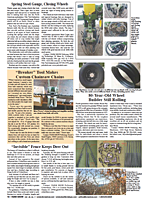
Click here to download page story appeared in.
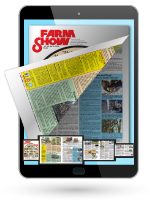
Click here to read entire issue
To read the rest of this story, download this issue below or click here to register with your account number.