1979 - Volume #3, Issue #2, Page #17
[ Sample Stories From This Issue | List of All Stories In This Issue | Print this story
| Read this issue]
Self-Propelled Planter/Cultivator
![]() |
With a little help from Bruce Viker, Halstad, Minn., and some labor on your part, you could build one for that price. Viker did. In fact, he's built two such machines himself and has put them to rugged use on his 1,500 acre Red River Valley farm.
Outstanding features - such as air-controlled cultivation pressure which "floats cultivators through fields," and a segmented, independently controlled tool bar built right into the center of the machine - make this a unique do-it-yourself machine.
It's made from a conglomeration of parts, including a "slant-6" 225 cu. in. Dodge engine and the differential and transmission from a 1957 Massey "80" combine. "We were developing the machine with features that don't exist on any tractor, such as a 132 in. wheel base," says Vicker. "Basically, we started from scratch."
The self-propelled planter-cultivator he designed has power comparable to a 60 hp. tractor. "That's important in itself," Viker points out. "You can't buy mid-size tractors anymore and we use huge tractors to do little jobs because we don't have any choice. But I think it's ridiculous to wear out a $30,000 tractor for things like cultivating sugarbeets."
Planter units and the interchangeable cultivator shanks ride on row gang units in front of the drive wheels, below and a little ahead of the driver's seat. The driver never has to turn to look at equipment behind him.
"You're right on top of the action, and that's important with beets," says Viker. The two machines he built are set up for 12 22-in. rows, but could have been built for any other sizes.
Viker designed the machine's system that "floats" cultivators through the ground with downward air pressure. "It lets you adjust to ground conditions," he says. "To dig deeper in hard ground, you just up the pressure." He uses a small electric compressor, about the size used on adjustable automotive shock absorbers, to get the job done.
While air pressure is used for downward pressure, hydraulic pressure is used in the same cylinders to lift the row gang units out of the ground. They move up and back, like the fold in a child's swing.
Another feature of the plantercultivator is the short changeover from cultivation to planting. Just four bolts for every two rows to remove the shanks and mount the Nodet planting units.
The precision of Viker's machine is also important to him, especially when working beets. The toolbar is rigidly bolted to the machine and goes wherever the machine goes. As a guide, he uses rear-mounted cone discs that dig a groove when planting, and are followed by mono-ribbed front tires when cultivating.
Unlike most wide-front tractors, the rear wheels on Viker's machine are spaced 44 in. wider than the front wheels. "We did that to make sure the guiding grooves remain clear and distinct."
The planter-cultivator's gas tank is made of special rubber and mounted up front over the wheels. "That was the only place left to put it," says Viker.
An extra benefit Viker didn't expect is energy efficiency. Traveling 6 to 7 mph for most operations, he used about 21/2 gal. per hour, or about 12 to 13 acres per 21/2 gal. He attributes that to the machine's ability to float equipment through the ground.
Viker says the machine could be used in most any row crop although he has no plans to develop it commercially himself. It cost him about $2,500 to build, not counting his labor.
He'll share his design with anyone interested, although he'd prefer to be contacted by phone, not written.
For more information, call: Bruce Viker, Halstad, Minn. (ph 701 457-2201).
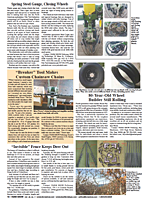
Click here to download page story appeared in.
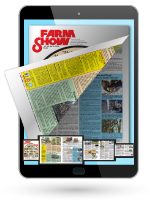
Click here to read entire issue
To read the rest of this story, download this issue below or click here to register with your account number.