Mini Hammermill Chops Up Garden Nutrients
Ron Hein's homemade mini hammermill makes great plant food. It grinds up horse manure and other material so it's easy to spread and breaks down fast in the soil. The 35-in. long, 16-in. wide hammermill is easy to transport with a tow bar on it, and can be maneuvered around with drop down handles.
"When we clear out a garden bed in the fall, we run the material through the hammermill along with horse or cow manure, spread it and till," says Hein. "By spring it's ready to plant, and in our dry climate, that organic matter helps hold moisture, too."
Hein fabricated a frame out of unistrut channel and 2 by 2 3/16-in. angle iron. The 1 5/8-in. unistrut channels are pre-drilled with holes every 2 in. The C-shaped channel has special fasteners designed to slide inside the channel, making it ideal as a subframe for mounting the drive engine.
"Unistruts make it easy to slide the engine sideways or back and forth," he says.
Hein also used unistruts for the legs. Angle iron was used for the long frame members to mount the engine subframe and the hammermill with hopper.
The 14 hammers in the mill are 2 by 6 by 1/4-in. mild steel plates that Hein hard-surfaced with a surfacing compound. The half-pound hammers are mounted to a 1 1/4-in. square shaft. The shaft is mounted to the angle iron frame with pillow block bearings.
Each hammer is bolted to a set of steel "ears." As they wear, they can be turned and flipped to expose new edges.
"Welding the ears and balancing the hammers was the trickiest part of the building process," says Hein. "They have to be perfectly balanced or the shaft will torque out of shape. Each hammer was punch pressed and jigged to be exactly the same size."
The hammers pass through a set of 6 knives cut from worn out tillage blades. Hein used a hydraulic press to flatten them and then sharpen them. The knives are fastened to a steel plate base with Grade 8 bolts and nylon lock nuts to secure knives and hammers alike. As the knives wear, like the hammers, they can be turned three times to expose fresh corner edges.
A 5 1/2 hp Honda engine with a centrifugal clutch powers the hammermill. The go-cart style engine and clutch simplifies controls and operation. At idle, the hammers hang in place. As the throttle advances, the clutch engages, and the hammers begin to spin.
The 14 by 16-in. hinged hopper made with 16-ga. sheet metal widens to a 16 by 20-in. mouth. It fits over the top of the hammers. The hopper mouth has a pipe rim rail around it. A piece of sheet metal was fabricated to slide onto the rim and cover up to half the hopper mouth. A rubber flap attached to it hangs down into the hopper, keeping material that is bouncing off the hammers and knives from being thrown back out of the hopper. The hopper is hinged at the rear end of the frame. When tipped open, a free-swinging leg hinged to the side of the hopper serves as a support.
Hein used a hydraulic press to form grates with various spacings for different levels of grind from fine to coarse. For a first pass with extremely clumpy material such as cow manure, he will often remove the grate entirely.
The grate profiles bring them to within 3/8 in. of the hammers. Grates are hinged at the rear of the frame and easily removed. Two chains fastened at the rear of the frame pull the grates into place and secure them to the frame.
"The second hand engine and clutch cost about $300, but most of the rest was scrap left over from other projects or given to me," says Hein. "I spent about a month and a half just drafting the plans."
All moving parts on the unit are shielded for safety. Hein emphasizes the importance of wearing safety glasses and hearing protectors when working with a hammermill like his.
Hein may offer a "do it yourself" info packet for a fee if there's enough interest.
Contact: FARM SHOW Followup, Ron Hein, 4475 Meridian Rd., Peyton, Colo. 80831.
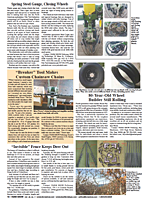
Click here to download page story appeared in.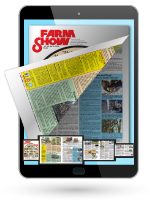
Click here to read entire issue
Mini Hammermill Chops Up Garden Nutrients CROPS Miscellaneous Ron Hein s homemade mini hammermill makes great plant food It grinds up horse manure and other material so it s easy to spread and breaks down fast in the soil The 35-in long 16-in wide hammermill is easy to transport with a tow bar on it and can be maneuvered around with drop down handles When we clear out a garden bed in the fall we run the material through the hammermill along with horse or cow manure spread it and till says Hein By spring it s ready to plant and in our dry climate that organic matter helps hold moisture too Hein fabricated a frame out of unistrut channel and 2 by 2 3/16-in angle iron The 1 5/8-in unistrut channels are pre-drilled with holes every 2 in The C-shaped channel has special fasteners designed to slide inside the channel making it ideal as a subframe for mounting the drive engine Unistruts make it easy to slide the engine sideways or back and forth he says Hein also used unistruts for the legs Angle iron was used for the long frame members to mount the engine subframe and the hammermill with hopper The 14 hammers in the mill are 2 by 6 by 1/4-in mild steel plates that Hein hard-surfaced with a surfacing compound The half-pound hammers are mounted to a 1 1/4-in square shaft The shaft is mounted to the angle iron frame with pillow block bearings Each hammer is bolted to a set of steel ears As they wear they can be turned and flipped to expose new edges Welding the ears and balancing the hammers was the trickiest part of the building process says Hein They have to be perfectly balanced or the shaft will torque out of shape Each hammer was punch pressed and jigged to be exactly the same size The hammers pass through a set of 6 knives cut from worn out tillage blades Hein used a hydraulic press to flatten them and then sharpen them The knives are fastened to a steel plate base with Grade 8 bolts and nylon lock nuts to secure knives and hammers alike As the knives wear like the hammers they can be turned three times to expose fresh corner edges A 5 1/2 hp Honda engine with a centrifugal clutch powers the hammermill The go-cart style engine and clutch simplifies controls and operation At idle the hammers hang in place As the throttle advances the clutch engages and the hammers begin to spin The 14 by 16-in hinged hopper made with 16-ga sheet metal widens to a 16 by 20-in mouth It fits over the top of the hammers The hopper mouth has a pipe rim rail around it A piece of sheet metal was fabricated to slide onto the rim and cover up to half the hopper mouth A rubber flap attached to it hangs down into the hopper keeping material that is bouncing off the hammers and knives from being thrown back out of the hopper The hopper is hinged at the rear end of the frame When tipped open a free-swinging leg hinged to the side of the hopper serves as a support Hein used a hydraulic press to form grates with various spacings for different levels of grind from fine to coarse For a first pass with extremely clumpy material such as cow manure he will often remove the grate entirely The grate profiles bring them to within 3/8 in of the hammers Grates are hinged at the rear of the frame and easily removed Two chains fastened at the rear of the frame pull the grates into place and secure them to the frame The second hand engine and clutch cost about $300 but most of the rest was scrap left over from other projects or given to me says Hein I spent about a month and a half just drafting the plans All moving parts on the unit are shielded for safety Hein emphasizes the importance of wearing safety glasses and hearing protectors when working with a hammermill like his Hein may offer a do it yourself info packet for a fee if there s enough interest Contact: FARM SHOW Followup Ron Hein 4475 Meridian Rd Peyton Colo 80831
To read the rest of this story, download this issue below or click
here to register with your account number.