This Livestock Chute Built To Last
When Larry Olson built a loading chute for his hogs, he built it to last and included all the bells and whistles he could. Olson had been building chutes for others and planned to stop with a last one for himself. He admits he rather outdid himself with a design that makes it as easy to bring feeder pigs in as it does to load them out at finish. And it makes clean up even easier.
“I had never built one like this,” he says. “It ended up costing twice as much as I expected. Materials alone ran at least $8,000.”
The lighted chute consists of a 32-in. wide walkway for pigs with an 18-in. walkway alongside for people. Its 6 1/2-ft. height gives plenty of clearance, and the 28-ft. length lets pigs climb up or down even from the highest point of a triple deck trailer.
A light steel roof over both walkways keeps pigs and people out of the weather. Accordion-like hoods at either end adjust to match respective doorways for a windproof connection. The chute sides are 16-ga. steel, and the floor is 14 ga.
“I worked with a local steel yard that cut and fabricated the steel to my plan,” says Olson. “They formed the side panels with V’s or ridges to add strength.”
A scissor hoist with two 4-in. dia., 30-in. stroke cylinders raises the chute to 11 1/2 ft. The load-out (or in) platform at the upper end of the chute is raised by a single action cylinder (lowers by gravity) to keep it level with the truck floor when the angle of the chute changes.
The platform is designed with a twin layer floor under the load-out doorway. A double action cylinder extends the upper layer with the three-panel doorway when a little more reach is needed.
“The floor extension means we don’t have to back the truck up tight to the chute,” explains Olson. “The accordion curtain between the load-out doorway and the chute keeps the connection weather tight.”
The load-out platform doorway is equally versatile with two side panels hinged to uprights at the “truck end” of the platform. By pulling pins at the chute end, either panel can be turned to form a 45-degree angle bend in the end of the chute.
“The moveable panels let us load out straight from the chute or to the left or right of the platform,” says Olson.
Olson designed the framing for the chute with 2 by 2-in. square tubing for the sides and 3-in. angle iron and tubing under the floor. The scissor hoist lifts against a frame of 3 by 3-in. square tubing that also anchors the axle and two 3 by 3-in. outriggers on 3-in., 8-in. stroke hydraulic cylinders.
“The hydraulics are all self-contained with an electric hydraulic pump,” says Olson. “All I have to do is plug it into a 110-volt outlet, and the hydraulics and interior lighting are all functional.”
The floor panels have 1 by 1-in. square tubing fastened to them at 4-ft. intervals. They provide periodic foot holds for young pigs being delivered. They also provide supports for expanded metal panels that are hinged to one side of the chute floor.
“When we are loading pigs out, we lower the expanded metal panels to provide them with secure footing,” explains Olson. “When we are bringing young pigs in, we lift them so they can’t get footing to turn around and go back up the chute.”
The expanded metal also lifts out of the way for easy cleaning. “We wash it out after every use,” says Olson. “I hope it will last a long time.”
Contact: FARM SHOW Followup, Larry D. Olson, Laneview Farm, 1956 190th St., Clarion, Iowa 50525 (ph 515 689-3506).
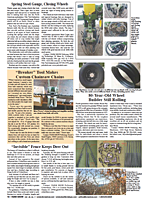
Click here to download page story appeared in.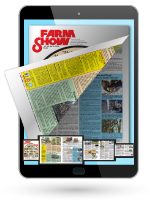
Click here to read entire issue
This Livestock Chute Built To Last LIVESTOCK Beef When Larry Olson built a loading chute for his hogs he built it to last and included all the bells and whistles he could Olson had been building chutes for others and planned to stop with a last one for himself He admits he rather outdid himself with a design that makes it as easy to bring feeder pigs in as it does to load them out at finish And it makes clean up even easier “I had never built one like this ” he says “It ended up costing twice as much as I expected Materials alone ran at least $8 000 ” The lighted chute consists of a 32-in wide walkway for pigs with an 18-in walkway alongside for people Its 6 1/2-ft height gives plenty of clearance and the 28-ft length lets pigs climb up or down even from the highest point of a triple deck trailer A light steel roof over both walkways keeps pigs and people out of the weather Accordion-like hoods at either end adjust to match respective doorways for a windproof connection The chute sides are 16-ga steel and the floor is 14 ga “I worked with a local steel yard that cut and fabricated the steel to my plan ” says Olson “They formed the side panels with V’s or ridges to add strength ” A scissor hoist with two 4-in dia 30-in stroke cylinders raises the chute to 11 1/2 ft The load-out or in platform at the upper end of the chute is raised by a single action cylinder lowers by gravity to keep it level with the truck floor when the angle of the chute changes The platform is designed with a twin layer floor under the load-out doorway A double action cylinder extends the upper layer with the three-panel doorway when a little more reach is needed “The floor extension means we don’t have to back the truck up tight to the chute ” explains Olson “The accordion curtain between the load-out doorway and the chute keeps the connection weather tight ” The load-out platform doorway is equally versatile with two side panels hinged to uprights at the “truck end” of the platform By pulling pins at the chute end either panel can be turned to form a 45-degree angle bend in the end of the chute “The moveable panels let us load out straight from the chute or to the left or right of the platform ” says Olson Olson designed the framing for the chute with 2 by 2-in square tubing for the sides and 3-in angle iron and tubing under the floor The scissor hoist lifts against a frame of 3 by 3-in square tubing that also anchors the axle and two 3 by 3-in outriggers on 3-in 8-in stroke hydraulic cylinders “The hydraulics are all self-contained with an electric hydraulic pump ” says Olson “All I have to do is plug it into a 110-volt outlet and the hydraulics and interior lighting are all functional ” The floor panels have 1 by 1-in square tubing fastened to them at 4-ft intervals They provide periodic foot holds for young pigs being delivered They also provide supports for expanded metal panels that are hinged to one side of the chute floor “When we are loading pigs out we lower the expanded metal panels to provide them with secure footing ” explains Olson “When we are bringing young pigs in we lift them so they can’t get footing to turn around and go back up the chute ” The expanded metal also lifts out of the way for easy cleaning “We wash it out after every use ” says Olson “I hope it will last a long time ” Contact: FARM SHOW Followup Larry D Olson Laneview Farm 1956 190th St Clarion Iowa 50525 ph 515 689-3506
To read the rest of this story, download this issue below or click
here to register with your account number.