You have reached your limit of 3 free stories. A story preview is shown instead.
To view more stories
(If your subscription is current,
click here to Login or Register.)
Built-From-Scratch Walk-In "Freezer Building"
When his CSA and farmers market meat sales outgrew 2 conventional walk-in freezers, Forrest Pritchard decided to put up a “freezer building”. His Smith Meadows farm is a grass-finished livestock farm that markets beef, lamb, pork and chicken. Pritchard describes the project on his website blog and gave FARM SHOW permis
..........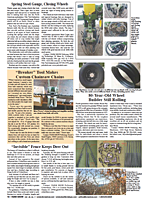
You must sign in, subscribe or renew to see the page.
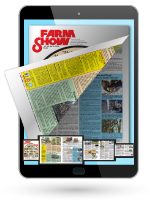
You must sign in, subscribe or renew to see the flip-book
Built-From-Scratch Walk-In Freezer Building BUILDINGS Miscellaneous When his CSA and farmers market meat sales outgrew 2 conventional walk-in freezers Forrest Pritchard decided to put up a “freezer building” His Smith Meadows farm is a grass-finished livestock farm that markets beef lamb pork and chicken Pritchard describes the project on his website blog and gave FARM SHOW permission to adapt it here “On a basic level a standard 18-cu ft refrigerator and a 3 200-cu ft walk-in freezer are remarkably similar ” says Pritchard “They both depend on insulation compressors refrigerant and blowers to function ” Essentially it is an interior box surrounded by an insulated box and an exterior Pritchard did much of the work himself using 2 by 4 construction and help from 2 sets of specialists Footings were laid out excavated and poured Once the concrete block was laid the first variation on standard construction occurred “We laid out 4-in pipe spaced at 4-ft intervals under the area to be covered by the concrete pad ” says Pritchard The tubes protrude through the block walls to exterior breather caps that allow warm air to flow down the tubes and beneath the slab This keeps the penetrating cold from the freezer above from heaving the subsoil and cracking the concrete A layer of gravel was laid over the pipes to drain water away It also provided a level area for the insulating foam subsurface laid down by his first set of specialists Made partially of soy the insulation was blown in a 4-in thick sheet several inches above the footings “Once cured 2 days at 70°F it became very firm extremely rigid says Pritchard We poured the 22 by 20-ft concrete slab over it The slab is the floor of the freezer and was treated with an anti-slip epoxy sealer Two sets of stud walls were built spaced 6 in apart One sets on the slab and makes up the inside box The other directly above the footings formed the outside box with the roof set on it Once the interior sheathing was installed foam was sprayed against it from the outside It filled both sets of stud walls covered the ceiling and tied into the exposed foam beneath the slab The combination of offset walls and exposed foam ensures that a solid sheet of insulation with no conductive breaks enclose the interior box With the addition of exterior sheathing and glass board for a sanitary surface on the inside Pritchard brought in his second set of specialists They installed the wiring compressors and evaporators to make the freezer something more than a well-insulated box We built it with a 60-in door to accommodate a pallet jack says Pritchard If everything goes as planned it should serve our farm for many decades The 3 200-cu ft freezer was designed to house thousands of pounds of beef pork lamb and chicken raised at Smith Meadows Pritchard says the entire project cost $45 000 in labor and materials and was funded entirely through sales at farmers markets Contact: FARM SHOW Followup Smith Meadows 568 Smithfield Lane Berryville Va 22611 ph 540 955-4389; info@smithmeadows com; www smithmeadows com
To read the rest of this story, download this issue below or click
here to register with your account number.