2019 - Volume #43, Issue #3, Page #34
[ Sample Stories From This Issue | List of All Stories In This Issue | Print this story
| Read this issue]
“Crusher” Flattens Filters Fast
![]() |
![]() |
“I couldn’t find a commercial filter crusher that was fast enough, tough enough, or big enough for my needs so I built my own,” says McLaen. “In about 20 seconds, it will crush most automotive filters down to about 1 1/2 in. and most truck filters down to 4 in.”
McLaen fabricated the crushing chamber out of 7 by 7-in., 1/4-in. steel tubing. A 6 by 6-in., 3/8-in. square tube piston and a 4 by 9-in. hydraulic cylinder fit inside the chamber. The piston is shimmed with 2 strips of 1/8-in. thick steel on each of its four sides to keep it from binding in the slightly larger chamber.
The cylinder pins to clevis-like ears on a plate that fits in the top of the chamber. Two pieces of channel iron are welded to the top of the plate.
“I drilled 2 sets of holes at the top of the chamber for pins that slide through the chamber walls and the channel iron,” says McLaen. “The pins let me take the plate out or raise it for taller filters by slipping them in the top pair of holes.”
An access hole in the side near the bottom of the piston lets McLaen pin the cylinder ram to ears welded to a steel plate welded to the bottom of the piston.
“Pinning the different components together makes it easy to service the crusher if needed,” says McLaen.
Most of the steel came from McLaen’s scrap pile or that of a neighbor. The hydraulic cylinder came from an online surplus center, and a local NAPA dealer made the hoses.
“I power it with the auxiliary valve on my skid steer, but any hydraulic pump or set of remotes would do,” says McLaen. “Oil from the crushed filters drains out of a 1-in. hole in the bottom of the chamber and into a catch pail.”
The entire crushing unit is mounted on wheels, with the chamber mounted high enough that McLaen doesn’t have to bend over to slip filters through the access door. “I can move it out into the open when there are a bunch of filters to crush and out of the way, when it isn’t needed,” says McLaen. “I can crush 3 small filters or 2 large ones at a time.”
He fabricated it in his spare time over a couple of weeks. Oil from the crushed filters is burned in the shop’s waste oil furnace, and the metal is recycled.
“It was fun to build and is even more fun to operate,” says McLaen. “The total cost was about $900, and most of that was hydraulics.”
Contact: FARM SHOW Followup, Dale McLaen, McLaen’s Service, 13756 Hwy. 11, Rutland, N. Dak. 58067 (ph 701 724-6232; mclaen@drtel.net).
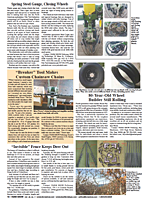
Click here to download page story appeared in.
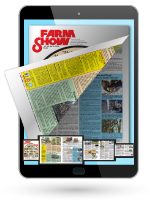
Click here to read entire issue
To read the rest of this story, download this issue below or click here to register with your account number.