You have reached your limit of 3 free stories. A story preview is shown instead.
To view more stories
(If your subscription is current,
click here to Login or Register.)
Jig Speeds Rotary Hoe Repair
Paul Bickford likes the weed control his rotary hoe provides. His homemade jig for replacing worn out spoke or tooth tips with Ho-Bit spoons (Vol. 41, No. 2) makes it even better.
“I have an older, 30-ft. rotary hoe, but if I had one new from the factory, I still would add the Ho-Bits,” says Bickford. “They are
..........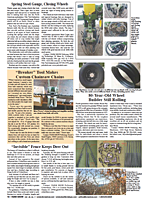
You must sign in, subscribe or renew to see the page.
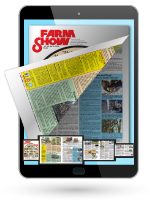
You must sign in, subscribe or renew to see the flip-book
Jig Speeds Rotary Hoe Repair CULTIVATORS Paul Bickford likes the weed control his rotary hoe provides His homemade jig for replacing worn out spoke or tooth tips with Ho-Bit spoons Vol 41 No 2 makes it even better “I have an older 30-ft rotary hoe but if I had one new from the factory I still would add the Ho-Bits ” says Bickford “They are wider and provide more of a cup effect than the original tips They really rip up the dirt ” New hoe or not accurately placing replacement spoons at the end of the spokes is key Rotary hoes are often used to remove weeds by stirring the soil surface without disturbing the germinating seed below Too long or too short and they won’t do the job “We tried a vise grip to hold individual spoons in place but we didn’t get consistent placement ” says Bickford “The Ho-Bits came with a jig but we found it cumbersome ” When an employee suggested an alternative Bickford went for it What they came up with was a framework of salvaged steel that allows the rotary hoe wheel to spin in place with a spoon holder that can pivot into position for welding the Ho-Bit in place A vertical leg of 2 by 2-in steel tube is topped by a headless 5/8-in bolt at a comfortable working height “The wheel slides onto the bolt and is held in place with a nut ” explains Bickford “If there is play in the wheel it usually means we need to replace the bearing as well as the tips ” A horizontal tube extends forward from the wheel holder and provides a base for a length of broken-off axle The axle pivots inside a bushing welded in a vertical position to the steel tube The actual spoon holder is a short length of steel welded to the upper end of the axle A cradle for holding a Ho-Bit is at the other end A stop on the horizontal tube restricts rotation When rotated into place with a new Ho-Bit resting on the cradle the spoon holder aligns with an arm on the rotary hoe As the arm also rotates into place against the new spoon it is welded in place “Old tips can wear unevenly but the jig ensures the new spoons are all at the same distance from the center of the wheel ” says Bickford A spring attached to a nut at the lower end of the axle holds the spoon holder against the stop tab To speed the process washers sized to hold extra Ho-Bits were welded to the steel table alongside the jig Like everything else in the jig they came from the scrap pile “We just used scrap we had laying around but it works ” says Bickford “With extra spoons in the washers we can just go down the line bang bang bang Building the jig for just the one machine was worth it ” Contact: FARM SHOW Followup Paul Bickford Bickford Farms 3036 Ridgevue Rd Ridgeway Wis ph 608 574-2307; bickfarm@gmail com; www bickfordorganics com
To read the rest of this story, download this issue below or click
here to register with your account number.