Smaller Manure Digester For Family-Sized Dairies
Brian Langolf has a better idea for handling manure on family-sized dairies - turn it into energy. The University of Wisconsin (UW) Oshkosh researcher helped set up a modular system at a nearby 135-cow dairy to produce biogas. It fuels a 64 kW CHP (combined heat and power) generator.
“There are 42 larger digesters in place at dairies around Wisconsin, but all but two are larger operations,” says Langolf, director, Biogas Systems and Research Development, UW Oshkosh. “This one is unique as there are only three digesters in the entire U.S. for herds with less than 200 cows.”
The 2,400-sq. ft. system is set up in units that look a bit like extra large shipping containers. It consists of two 40,000-gal. fermentation vessels, a feeding hopper and the CHP system. It produces 25,900 cu. ft. per day of biogas and 481,800 kWh of electricity per year, enough electricity for 40 homes and enough heat for 61 homes. The electricity is sold, and the heat produced is used in the biogas production system and at the farm.
The current facility can handle up to 200 cows. The design can accommodate a third fermentation vessel for an even larger herd.
Langolf serves on the board of directors of the American Biogas Council. He says there has been a surge of interest in biogas production and building new digesters. He explains that there are multiple benefits to digesters for smaller farms.
“Right now, a lot of people are looking at digesters to convert biogas into renewable natural gas (RNG) for vehicle fuel,” says Langolf. “If you look at it holistically, you can use the residue for bedding, produce value added (pathogen/odor reduced) soil amendments that would provide better crop nutrients, and produce renewable fuel.”
Langolf notes that it is hard to put a figure on cost savings and benefits other than electricity and/or RNG sales. However, that is what this project is attempting to do.
Digester feed products include 6,500 tons per year of liquid manure, solid bedding and crop residue, as well as food waste from a nearby food processor. Tipping fees from the food waste is part of the revenue stream.
“Our goal is to divert food waste and other organics from the landfill to higher value uses, such as renewable energy generation,” says Langolf.
System components came from a variety of research partners, including BIOFerm energy systems, a German company.
“This size of digester is more typical in Germany,” explains Langolf.
The entire system required an investment of $1.2 million by the university, the state of Wisconsin and Wisconsin Public Service (electric and gas utility).
Contact: FARM SHOW Followup, Biogas Systems, 800 Algoma Blvd., Oshkosh, Wis. 54901 (ph 920 424-0767; langolfb@uwosh.edu; www.uwosh.edu/biogas/).
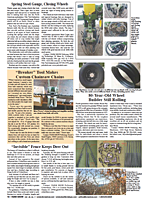
Click here to download page story appeared in.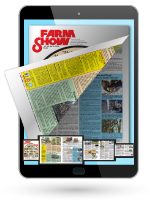
Click here to read entire issue
Smaller Manure Digester For Family-Sized Dairies DAIRY EQUIPMENT & IDEAS Brian Langolf has a better idea for handling manure on family-sized dairies - turn it into energy The University of Wisconsin UW Oshkosh researcher helped set up a modular system at a nearby 135-cow dairy to produce biogas It fuels a 64 kW CHP combined heat and power generator “There are 42 larger digesters in place at dairies around Wisconsin but all but two are larger operations ” says Langolf director Biogas Systems and Research Development UW Oshkosh “This one is unique as there are only three digesters in the entire U S for herds with less than 200 cows ” The 2 400-sq ft system is set up in units that look a bit like extra large shipping containers It consists of two 40 000-gal fermentation vessels a feeding hopper and the CHP system It produces 25 900 cu ft per day of biogas and 481 800 kWh of electricity per year enough electricity for 40 homes and enough heat for 61 homes The electricity is sold and the heat produced is used in the biogas production system and at the farm The current facility can handle up to 200 cows The design can accommodate a third fermentation vessel for an even larger herd Langolf serves on the board of directors of the American Biogas Council He says there has been a surge of interest in biogas production and building new digesters He explains that there are multiple benefits to digesters for smaller farms “Right now a lot of people are looking at digesters to convert biogas into renewable natural gas RNG for vehicle fuel ” says Langolf “If you look at it holistically you can use the residue for bedding produce value added pathogen/odor reduced soil amendments that would provide better crop nutrients and produce renewable fuel ” Langolf notes that it is hard to put a figure on cost savings and benefits other than electricity and/or RNG sales However that is what this project is attempting to do Digester feed products include 6 500 tons per year of liquid manure solid bedding and crop residue as well as food waste from a nearby food processor Tipping fees from the food waste is part of the revenue stream “Our goal is to divert food waste and other organics from the landfill to higher value uses such as renewable energy generation ” says Langolf System components came from a variety of research partners including BIOFerm energy systems a German company “This size of digester is more typical in Germany ” explains Langolf The entire system required an investment of $1 2 million by the university the state of Wisconsin and Wisconsin Public Service electric and gas utility Contact: FARM SHOW Followup Biogas Systems 800 Algoma Blvd Oshkosh Wis 54901 ph 920 424-0767; langolfb@uwosh edu; www uwosh edu/biogas/
To read the rest of this story, download this issue below or click
here to register with your account number.