Self-Taught Machinist Builds Brass Clock
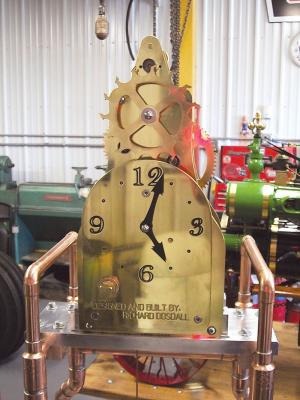 ✖  |
Rich Dosdall is detail oriented to the nth degree, a dedicated self-taught woodworker and machinist who’s produced thousands of intricate hand-made parts over 30 years. Those parts have been used for restoring tractors, building replica steam engines, and even making parts for brass clocks.
“By 10th grade, I was a fairly good woodworker and had made gun cabinets, roll-top desks, coffee tables, kitchen and bathroom cabinets, and more. In 11th grade, I started building grandfather clocks and did that as a hobby for about 10 years, and then repaired them for several years after that,” Dosdall says. “Eventually, my clock suppliers went out of business, so I thought it would be fun to build a clock of my own design from scratch. Everyone told me I was crazy to try it, but that just inspired me to prove I could do it.”
Dosdall’s clock project evolved over several months. He used 1/4-in. brass for the side plates and fitted every shaft with a ball or needle bearing of his design. He cut all the gears himself and used his CNC machine to engrave the dial. For the escapement, he copied a design from an 1850’s pocket watch and scaled it up to the size he needed. The pendulum is a huge 4-in. brass valve that’s half the size of a loaf of bread. It’s supported by an eye hook linked to a copper cable that operates the clock mechanism. The valve is filled with lead shot to achieve the exact weight needed for continuous operation.
The stand is equally impressive, made of 1-1/4 in. copper pipe configured into a sturdy box shape that’s 2 ft. wide, 2 ft. deep, and 5 ft. tall.
Dosdall says he thought about mounting the mechanism in a wood case, but then the intricate handiwork on the clock would’ve been hidden.
Dosdall says he built the clock in 4 to 5 mos. and spent about $400 on materials. It was an interesting project, but not one that he’s replicated. He prefers building motorized equipment or refurbishing old farm tractors back to their original condition, especially if those projects involve making specialized replacement parts.
Contact: FARM SHOW Followup, Rich Dosdall, Red Wing, Minn. (mailman50@hughes.net).
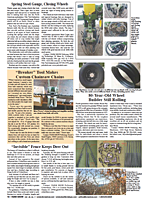
Click here to download page story appeared in.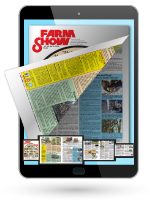
Click here to read entire issue
Self-Taught Machinist Builds Brass Clock AG WORLD Rich Dosdall is detail oriented to the nth degree a dedicated self-taught woodworker and machinist who’s produced thousands of intricate hand-made parts over 30 years Those parts have been used for restoring tractors building replica steam engines and even making parts for brass clocks “By 10th grade I was a fairly good woodworker and had made gun cabinets roll-top desks coffee tables kitchen and bathroom cabinets and more In 11th grade I started building grandfather clocks and did that as a hobby for about 10 years and then repaired them for several years after that ” Dosdall says “Eventually my clock suppliers went out of business so I thought it would be fun to build a clock of my own design from scratch Everyone told me I was crazy to try it but that just inspired me to prove I could do it ” Dosdall’s clock project evolved over several months He used 1/4-in brass for the side plates and fitted every shaft with a ball or needle bearing of his design He cut all the gears himself and used his CNC machine to engrave the dial For the escapement he copied a design from an 1850’s pocket watch and scaled it up to the size he needed The pendulum is a huge 4-in brass valve that’s half the size of a loaf of bread It’s supported by an eye hook linked to a copper cable that operates the clock mechanism The valve is filled with lead shot to achieve the exact weight needed for continuous operation The stand is equally impressive made of 1-1/4 in copper pipe configured into a sturdy box shape that’s 2 ft wide 2 ft deep and 5 ft tall Dosdall says he thought about mounting the mechanism in a wood case but then the intricate handiwork on the clock would’ve been hidden Dosdall says he built the clock in 4 to 5 mos and spent about $400 on materials It was an interesting project but not one that he’s replicated He prefers building motorized equipment or refurbishing old farm tractors back to their original condition especially if those projects involve making specialized replacement parts Contact: FARM SHOW Followup Rich Dosdall Red Wing Minn mailman50@hughes net
To read the rest of this story, download this issue below or click
here to register with your account number.