You have reached your limit of 3 free stories. A story preview is shown instead.
To view more stories
(If your subscription is current,
click here to Login or Register.)
Wooden Conveyor Moves Firewood
Paul Zawalick loads firewood the easy way with his homemade wooden conveyor. With the hopper set beneath his cordwood saw, pieces of firewood travel up the 16 ft. length to a height of about 10 ft. to drop into trailers or truck beds parked beneath. A hitch at the ground level end makes it easy to move the wheeled conv
..........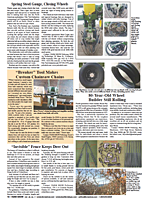
You must sign in, subscribe or renew to see the page.
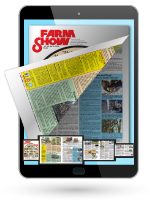
You must sign in, subscribe or renew to see the flip-book
Wooden Conveyor Moves Firewood WOOD STOVES/FURNACES Paul Zawalick loads firewood the easy way with his homemade wooden conveyor With the hopper set beneath his cordwood saw pieces of firewood travel up the 16 ft length to a height of about 10 ft to drop into trailers or truck beds parked beneath A hitch at the ground level end makes it easy to move the wheeled conveyor as needed “The conveyor length was limited to 16 ft because those were the longest 2 by 8-in treated boards available ” says Zawalick “I used two of them together for the floor of the conveyor and 3/4-in pressure-treated deck boards for the 45-degree angled sides ” Zawalick used standard roller chain for the conveyor apron chains with angle iron cross bars at 2 1/2-ft intervals “You can get apron chain with brackets for the cross bars but it’s more expensive so I just welded the angle iron to the chains ” he says “I used sprockets from an old-style hay loader The ones at the top of the conveyor are chain driven by a motor at the bottom ” When he first built the conveyor Zawalick powered it with a 7 6-hp Gravely lawn tractor with bolt jacks on either side to line it up with the chain drive “When I got rid of the Gravely I bought a small gas engine just 2 to 3 hp from Harbor Freight and a 90-degree gearbox ” says Zawalick “The gearbox is belt driven from the motor with a sprocket on it for the drive chain ” The drive chain runs half the length of the conveyor from the gearbox to a sprocket that acts as an idler Then it continues from there to the drive sprockets at the end of the conveyor “I like to keep the belt between the engine and the gearbox a little loose so if the conveyor jams up it’ll slip ” says Zawalik At the hopper end of the conveyor the shaft for the elevator apron sprockets is held in place by pillow block bearings The bearings are bolted to slots in lengths of channel iron The channel iron is welded to steel plates bolted to the 2 by 8-in floor of the conveyor “When I need to add tension to the apron chain I loosen the bolts and use a pry bar to slide the shaft away from the conveyor before retightening the bolts ” says Zawalick “I’ve found I don’t need much tension on the chains ” He mounted swivel wheels from a cyclone rake to the conveyor hopper to make it easy to slip it into place He uses a concrete block at the hopper end to counter the weight of the firewood at the top The conveyor body is supported at mid-length by a framework fabricated with 1 1/2-in square tubing The tubing starts at the axle with its wheelbarrow wheels and extends at least a foot above the conveyor as well as forward to the lower end of the conveyor Truss cables run on both sides of the conveyor from the top to the bottom with the top of the tubing as truss supports “The cable helps support the length of the conveyor when it’s loaded with firewood ” explains Zawalick “Also at the midpoint I have a crescent-shaped piece of wood mounted beneath the returning apron chain It helps keep the apron chain in place ” Contact: FARM SHOW Followup Paul Zawalick 545 Sylvester Rd Florence Mass 01062 ph 413-584-4162; J0236@comcast net
To read the rest of this story, download this issue below or click
here to register with your account number.