You have reached your limit of 3 free stories. A story preview is shown instead.
To view more stories
(If your subscription is current,
click here to Login or Register.)
Hydraulic “Wrench” Built For Big Jobs
When Dan Erdman needed to turn an oversized nut on a hydraulic cylinder, he used an oversized powered “wrench” that he made out of a hydraulic cylinder. Until he recently sold it, he used it for years, whenever he needed to crack a really big nut.
“I built it for breaking 4 to 5-in. nuts on large hydraulic cylin
..........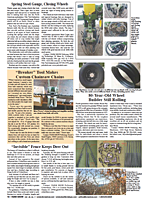
You must sign in, subscribe or renew to see the page.
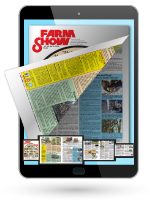
You must sign in, subscribe or renew to see the flip-book
Hydraulic “Wrench” Built For Big Jobs FARM SHOP Tools When Dan Erdman needed to turn an oversized nut on a hydraulic cylinder he used an oversized powered “wrench” that he made out of a hydraulic cylinder Until he recently sold it he used it for years whenever he needed to crack a really big nut “I built it for breaking 4 to 5-in nuts on large hydraulic cylinder rams when I needed to change the packing or rebuild a cylinder ” explains Erdman “Those nuts take a lot of torque ” Erdman put 8 by 8-in sq box steel tubing legs on either end of a 15-ft length of 12-in sq box tubing At the working end he welded a length of 8-in wide flange I-beam perpendicular to and centered on the leg It serves as a stabilizing foot for the leg and as a base for the cylinder/wrench Erdman fabricated an insert for the 12 by 12-in tubing to anchor the hydraulic cylinder that needed repair It consisted of two 3/4-in thick steel plates sized to fit inside the steel tubing with 4-in spacing between them They connected at one end with a large bracket He drilled holes in the center of the other ends and welded a steel rod in place “When I needed to work on a cylinder I slipped the clevis end over the rod and pinned it in place ” says Erdman “Then I pushed the insert and cylinder into the tubing ” The head of the hydraulic wrench is a 12 by 36-in 1-in thick steel plate Erdman drilled holes in all four corners of the plate and cut out a hole the size of the nut to be turned “I cut out a piece of cereal box the size of the nut and used it as a template to cut a hole in the 1-in steel plate ” says Erdman “Over time I cut multiple holes out of the plate to match different nut sizes ” To crack the nut Erdman would slip the plate with the hole over the nut Once he pinned the cylinder/wrench ram through a corner hole in the plate he could activate the cylinder As the ram extended the plate turned turning the nut as it did When the large cylinder repair was finished Erdman simply reversed the process to retighten the nut “I always marked the ramrod and the nut to bring it back to the right torque when reassembling ” says Erdman Contact: FARM SHOW Followup Dan Erdman Box 1620 Claresholm Alta Canada T0L 0T0 ph 403-382-1020; derdman2@telusplanet net
To read the rest of this story, download this issue below or click
here to register with your account number.