You have reached your limit of 3 free stories. A story preview is shown instead.
To view more stories
(If your subscription is current,
click here to Login or Register.)
Four-Cylinder Tabletop Engine Is A Work Of Art
Rich Dosdall says he’d never seen a 4-cyl. steam engine in all his years attending shows, auctions, and other events, so he decided to build one of his own design. With his imagination working overtime, the self-trained machinist, model builder, and craftsman built his “one-of-a-kind” work of art on a 32-in. wide by 4-
..........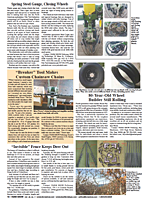
You must sign in, subscribe or renew to see the page.
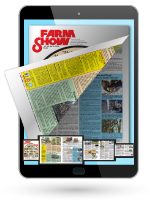
You must sign in, subscribe or renew to see the flip-book
Four-Cylinder Tabletop Engine Is A Work Of Art ENGINES Rich Dosdall says he’d never seen a 4-cyl steam engine in all his years attending shows auctions and other events so he decided to build one of his own design With his imagination working overtime the self-trained machinist model builder and craftsman built his “one-of-a-kind” work of art on a 32-in wide by 4-ft long tabletop platform The result is a compilation of all original parts assembled into a colorful engineering masterpiece that purrs like a kitten It’s identified by the hand-painted “Dosdall Engine Co ” nameplate and embossed “DE” letters on the ends of each cylinder housing Dosdall’s engineering marvel has four identical cylinders one on each corner of the platform Each piston has an elaborate housing and a machined rod connected to a central gear system Three gears in a pyramid shape are on each side The bottom two connect to the cylinders and the top gear of the trio links to a 16-in diameter flywheel in the center of the platform He machined authentic oil cups on the top of each shaft and railings on each cylinder with his CNC lathe Copper tubing runs from the make-believe two-story boiler room to each cylinder The second story of the boiler room even has a catwalk with brass railings Dosdall used all the machining tools in his extensive shop to produce the cylinders valves gears shafts mounting blocks pulleys and the authentic-looking brick smokestack “First I made wood patterns for all the parts then cast them from iron or machined them from steel The shiny 6-spoked flywheel is like others I’ve made for scale-model steam engines The bore and stroke of each cylinder is 2 1/2 by 3 Each cylinder has brass lagging to replicate the insulating jacket that keeps actual working steam-powered cylinders hot so the steam doesn’t condense ” Dosdall says “I run this engine on about 5 lbs of compressed air moving through a regulator that controls the piston speed Air is piped into each cylinder just like steam ” He has the pistons perfectly timed so there’s never a top dead center They run smoothly and only emit a small puff of air through the exhaust stack at the top of their compression cycle “Of all the parts on this project the 18-in tall chimney was the most time-consuming ” Dosdall says “I milled all the 1/8-in mortar lines with a dividing head then painted each one of those lines with a tiny brush I could only work on that for about 15 minutes at a time because of the eye strain ” Always a perfectionist in his work Dosdall says the project took him a full year to complete and he’s very satisfied with how it turned out “It has a little more gear noise than I’d like which could be remedied with gear lube but that’d create oil spatter that I’d rather do without ” Contact: FARM SHOW Followup Rich Dosdall Red Wing Minn mailman50@hughes net
To read the rest of this story, download this issue below or click
here to register with your account number.