Safer, More Precise Sandblasting Uses Less Sand
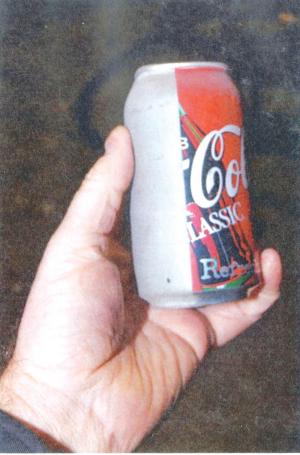 ✖  |
Jim Deardorff has been sandblasting metal for over 40 years and says more air and less pressure are better. Over that time, he developed a blasting system he refers to as Classic Blast (Vol. 26, No. 3). It’s one he continues to refine with emphasis on safe, low-pressure, low-impact blasting.
“Sand is used for scouring a metal surface to improve rust and paint removal because it’s cheap and readily available,” says Deardorff. “However, there are health concerns when high pressure (100 to 120 psi) breaks the sand crystals into fine dust. It can be inhaled and may cause respiratory problems.”
Deardorff still uses sand as one of his blasting mediums. The difference is he uses the Venturi effect to boost airflow without boosting pressure.
“I use a special double Venturi blast nozzle from Boride,” says Deardorff. “It has air induction holes that mix compressor air with up to 40 percent atmospheric air as it leaves the nozzle. This reduces the sand to air mixture, which reduces dust.”
Deardorff has also modified his 350-lb. Sandstorm sandblast pot to reduce sand use from 1,400 lbs. per hour to less than 200 lbs.
“I replaced the original air restrictor in the boot of the pot with a smaller one made by the company for smaller sandblast pots,” says Deardorff. “I also installed a moisture separator in the line that feeds media to the pot. It’s important to get all the moisture possible out of the media.”
Deardorff uses a 100 mesh to screen his media versus the 40 to 60 mesh screens used for most industrial media. He installed a gate valve with a pressure gauge on air entering the blast pot.
“I can adjust the air for the project with the gate valve and use the primary shutoff when starting or stopping,” he says. “I always record the pressure and the project for doing repeat projects.”
Much of Deardorff’s current work involves antique tractor and classic car parts. Recognizing that high pressure can damage these parts, he has reduced his blast pressure to 50 psi. It’s still enough to remove rust and old paint, thanks in part to a special blend of walnut shells and aluminum oxide he developed.
“It works great at low pressure,” says Deardorff. “With my system, I can recycle media up to 20 times.”
While working with his father, Deardorff built an air wash media cleaner. Used media feeds into a drawer on an incline. As it falls off the drawer, it passes through airflow that blows the contaminates up and out the top of the media cleaner. Reusable media falls to the bottom of the cleaner.
“With the media cleaner, I can add 50 lbs. a day to a batch of 800 to 1,000 lbs. of media and maintain media quality,” says Deardorff.
Since 1992, his low-pressure blasting technique has allowed Deardorff to prepare more than 200,000 parts fabricated from 20-gauge (less than 1/16-in.) thick steel.
“My customer powder-coats the parts, but they have to be rust-free,” says Deardorff. “Traditional high-pressure blasting would warp or distort the thin steel. My process removes rust without damage.”
When customers question his low-pressure process, he shows them how precise it is with a pop can that has had the paint removed from half the can.
“It proves to them that I can blast antique tractor or car parts, or nearly anything else, without warping, pitting, or excessive roughness,” says Deardorff.
Interested readers can contact Deardorff to receive a summary of his low-pressure, reusable media system.
Contact: FARM SHOW Followup, Jim Deardorff, Superior Coatings Co., 205 McCormick St., Chillicothe, Mo. 64601 (ph 660-646-6355; info@classicblast.com; www.classicblast.com).
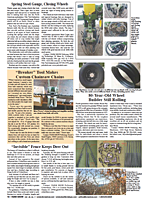
Click here to download page story appeared in.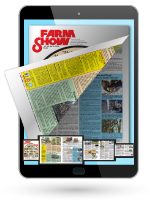
Click here to read entire issue
Safer More Precise Sandblasting Uses Less Sand FARM SHOP Miscellaneous Jim Deardorff has been sandblasting metal for over 40 years and says more air and less pressure are better Over that time he developed a blasting system he refers to as Classic Blast Vol 26 No 3 It’s one he continues to refine with emphasis on safe low-pressure low-impact blasting “Sand is used for scouring a metal surface to improve rust and paint removal because it’s cheap and readily available ” says Deardorff “However there are health concerns when high pressure 100 to 120 psi breaks the sand crystals into fine dust It can be inhaled and may cause respiratory problems ” Deardorff still uses sand as one of his blasting mediums The difference is he uses the Venturi effect to boost airflow without boosting pressure “I use a special double Venturi blast nozzle from Boride ” says Deardorff “It has air induction holes that mix compressor air with up to 40 percent atmospheric air as it leaves the nozzle This reduces the sand to air mixture which reduces dust ” Deardorff has also modified his 350-lb Sandstorm sandblast pot to reduce sand use from 1 400 lbs per hour to less than 200 lbs “I replaced the original air restrictor in the boot of the pot with a smaller one made by the company for smaller sandblast pots ” says Deardorff “I also installed a moisture separator in the line that feeds media to the pot It’s important to get all the moisture possible out of the media ” Deardorff uses a 100 mesh to screen his media versus the 40 to 60 mesh screens used for most industrial media He installed a gate valve with a pressure gauge on air entering the blast pot “I can adjust the air for the project with the gate valve and use the primary shutoff when starting or stopping ” he says “I always record the pressure and the project for doing repeat projects ” Much of Deardorff’s current work involves antique tractor and classic car parts Recognizing that high pressure can damage these parts he has reduced his blast pressure to 50 psi It’s still enough to remove rust and old paint thanks in part to a special blend of walnut shells and aluminum oxide he developed “It works great at low pressure ” says Deardorff “With my system I can recycle media up to 20 times ” While working with his father Deardorff built an air wash media cleaner Used media feeds into a drawer on an incline As it falls off the drawer it passes through airflow that blows the contaminates up and out the top of the media cleaner Reusable media falls to the bottom of the cleaner “With the media cleaner I can add 50 lbs a day to a batch of 800 to 1 000 lbs of media and maintain media quality ” says Deardorff Since 1992 his low-pressure blasting technique has allowed Deardorff to prepare more than 200 000 parts fabricated from 20-gauge less than 1/16-in thick steel “My customer powder-coats the parts but they have to be rust-free ” says Deardorff “Traditional high-pressure blasting would warp or distort the thin steel My process removes rust without damage ” When customers question his low-pressure process he shows them how precise it is with a pop can that has had the paint removed from half the can “It proves to them that I can blast antique tractor or car parts or nearly anything else without warping pitting or excessive roughness ” says Deardorff Interested readers can contact Deardorff to receive a summary of his low-pressure reusable media system Contact: FARM SHOW Followup Jim Deardorff Superior Coatings Co 205 McCormick St Chillicothe Mo 64601 ph 660-646-6355; info@classicblast com; www classicblast com
To read the rest of this story, download this issue below or click
here to register with your account number.