Chicken Compost Solves Problems And Makes Money
Mortalities and manure are facts of life when you keep 20,000 layer hens and roosters around. Disposing of 9 to 10-lb. dead chickens gets expensive, and Ed Rollins' fields couldn't handle any more chicken litter. When he looked into composting, he found answers to both problems and also discovered a new business opportunity.
"I was spending more than $3,700 each year on propane for an incinerator to dispose of the dead birds and another $600 each year on maintenance," says Rollins. "My fields had excess phosphate from years of spreading chicken litter on them."
Rollins produces fertile eggs under contract for the hatchery industry. Since he started composting, he also sells a trademarked product called R-Grow Organic Soil Conditioner. Sales through co-ops and Wal-Mart stores in Tennessee and neighboring states have added $30,000 to his gross income and $12,000 to his net income. It has also helped him employ a son and daughter in the business.
Another advantage of the composting operation is that Rollins can clean out his two laying buildings any time of the year. All chicken litter is stored in a 45 by 160-ft. composting facility. The roofed building has concrete floors and confinement walls. Eleven compost bins run down one side of the building, while separate areas are set aside for raw manure storage, aging compost staging, finished product storage and a bagging area.
"Each bin is 10 ft. wide, 5 1/2 ft. high and 12 ft. deep and holds 8 to 10 tons," says Rollins. "I premix the chicken litter and wood chips for the right carbon mix, and then every four days I layer it with about 300 lbs. of mortalities in a bin."
The exact recipe for the mix of manure, wood chips and dead chickens is not something Rollins shares, having achieved it only through lots of experimentation. Each batch of compost gets turned five times using a tractor and loader. It goes through four stages of cooking and cool downs, with the first reaching a temperature of 170?. The second stage hits 160?, the third 145?, and the final stage hits 140?. The compost cools to 130? in the first three stages and finally to 90? in the 25 by 50-ft. cooling bin before being chopped and bagged. The complete process lasts about 14 months with about 8 to 10 tons of finished compost produced every 20 days.
Before bagging, material is literally chopped into finer pieces by an old silage chopper that has been adapted to stationary use with a hopper feed. It blows the compost into the bagging area. A commercial bagging machine packages the compost in 22-lb. bags.
Rollins credits the University of Tennessee Center for Profitable Ag for helping him develop and fine-tune his process. He recommends people interested in developing an ag-related business, check with their state's university for a similar group.
Contact: FARM SHOW Followup, Ed Rollins, P.O. Box 324, Pulaski, Tenn. 38478 (ph 931 363-0265).
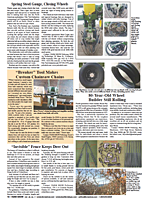
Click here to download page story appeared in.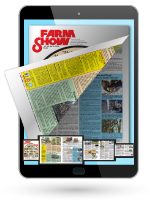
Click here to read entire issue
Chicken Compost Solves Problems And Makes Money SPECIALTY/SERVICES Specialty/Services 28-3-8 Mortalities and manure are facts of life when you keep 20,000 layer hens and roosters around. Disposing of 9 to 10-lb. dead chickens gets expensive, and Ed Rollins' fields couldn't handle any more chicken litter. When he looked into composting, he found answers to both problems and also discovered a new business opportunity.
"I was spending more than $3,700 each year on propane for an incinerator to dispose of the dead birds and another $600 each year on maintenance," says Rollins. "My fields had excess phosphate from years of spreading chicken litter on them."
Rollins produces fertile eggs under contract for the hatchery industry. Since he started composting, he also sells a trademarked product called R-Grow Organic Soil Conditioner. Sales through co-ops and Wal-Mart stores in Tennessee and neighboring states have added $30,000 to his gross income and $12,000 to his net income. It has also helped him employ a son and daughter in the business.
Another advantage of the composting operation is that Rollins can clean out his two laying buildings any time of the year. All chicken litter is stored in a 45 by 160-ft. composting facility. The roofed building has concrete floors and confinement walls. Eleven compost bins run down one side of the building, while separate areas are set aside for raw manure storage, aging compost staging, finished product storage and a bagging area.
"Each bin is 10 ft. wide, 5 1/2 ft. high and 12 ft. deep and holds 8 to 10 tons," says Rollins. "I premix the chicken litter and wood chips for the right carbon mix, and then every four days I layer it with about 300 lbs. of mortalities in a bin."
The exact recipe for the mix of manure, wood chips and dead chickens is not something Rollins shares, having achieved it only through lots of experimentation. Each batch of compost gets turned five times using a tractor and loader. It goes through four stages of cooking and cool downs, with the first reaching a temperature of 170?. The second stage hits 160?, the third 145?, and the final stage hits 140?. The compost cools to 130? in the first three stages and finally to 90? in the 25 by 50-ft. cooling bin before being chopped and bagged. The complete process lasts about 14 months with about 8 to 10 tons of finished compost produced every 20 days.
Before bagging, material is literally chopped into finer pieces by an old silage chopper that has been adapted to stationary use with a hopper feed. It blows the compost into the bagging area. A commercial bagging machine packages the compost in 22-lb. bags.
Rollins credits the University of Tennessee Center for Profitable Ag for helping him develop and fine-tune his process. He recommends people interested in developing an ag-related business, check with their state's university for a similar group.
Contact: FARM SHOW Followup, Ed Rollins, P.O. Box 324, Pulaski, Tenn. 38478 (ph 931 363-0265).
To read the rest of this story, download this issue below or click
here to register with your account number.