You have reached your limit of 3 free stories. A story preview is shown instead.
To view more stories
(If your subscription is current,
click here to Login or Register.)
Composter Bags A Bigger Market
When Carl Belohlavek turns his compost piles, he feels like he's turning leaves and grass clippings into dollar bills - lots of them.
The Mosinee, Wisconsin, entrepreneur got into the compost business as a way to generate more organic matter for his ginseng crop so he took in 80 truckloads of yard waste from the
..........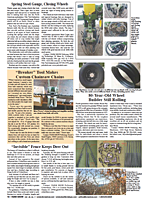
You must sign in, subscribe or renew to see the page.
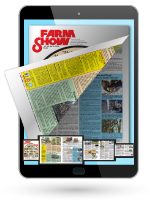
You must sign in, subscribe or renew to see the flip-book
Composter Bags A Bigger Market SPECIALTY/SERVICES Specialty/Services 28-3-8 When Carl Belohlavek turns his compost piles, he feels like he's turning leaves and grass clippings into dollar bills - lots of them.
The Mosinee, Wisconsin, entrepreneur got into the compost business as a way to generate more organic matter for his ginseng crop so he took in 80 truckloads of yard waste from the city that needed a home. It went so well he got rid of the ginseng crop and built a composting business that is growing bigger every year.
"I make about 1,200 cubic yards a year," says Belohlavek. "I sell most of it bulk, delivered anywhere in the state. We also sell by the bag. Some greenhouses take 400 to 800 bags at a time."
Belohlavek also sells compost through local hardware stores and services stations. These local sales have grown as people who try it come back for more.
""People who used to buy a half a yard or so, now want 4 to 8 yards after seeing how it helps their gardens," he says. He credits his master gardener wife Dorothy with creating the ultimate sales tool. "She has garden beds that are the envy of everyone who sees them, and they want the same for themselves."
It takes about three months to produce finished compost. Belohlavek stacks the material, sometimes using alfalfa for added nitrogen to meet the proper ratio of carbon to nitrogen. Once the compost is ready, he has a commercial screener come in to screen the compost. Material to be sold in 25-lb. bags is run through a home-built bagger. He can do 100 bags an hour by himself or 150 an hour with help.
The bagger bin holds 2 1/2 yards, more than needed to handle a 2-yard payloader bucket. It is made from 1/4-in. steel plate and supported on four 4-in. angle iron posts, ending in angle iron skids on the ground. The long sides of the bin slope to an auger mounted at the bottom.
"I cut a 6-in. diameter pipe in half, spread it and welded the bin sides to it and set the auger inside it," says Belohlavek.
A 4 by 8-ft. platform about 18 inches off the ground holds a 10 hp Honda motor and the hydraulic pump it powers, as well as a scale for weighing bags. Both the auger that runs along the bottom of the bin and a beater mounted about a foot above the auger to prevent bridging of material run on hydraulic motors. Both the beater and the auger can run in forward or reverse, and the auger has a speed control on it.
"Hydraulics are great to work with," says Belohlavek. "When I have a bag in place over the scale, I pull a lever to engage the auger and again to stop it when the scale hits 25 lbs."
Belohlavek bought the auger, but built the beater from 2-in. schedule 80 pipe with flat bars welded across it. Most of the bagger was built from scrap or used steel. Wheels that slide into place when one end of the bagger is lifted were cut down from a trailer house axle. They make it easier to move the bagger from a nearby shed.
"With the hydraulic motors and pump and a few other things, I probably have $600 to $700 in it, plus labor," says Belohlavek, who also built his own compost turner. "I like building things."
He's getting ready to expand his operation. A Wisconsin paper mill recently asked him to handle their wastes. He is busy building a new and larger composter to handle as much as 80,000 yards of compost per year. "I have a partnership with two guys to truck and sell the finished compost," he says. "We already have markets set up to sell a lot of it."
Contact: FARM SHOW Followup, Carl Belohlavek, RFD 3, Mosinee, Wis. 54455 (ph 715 693-3755).
To read the rest of this story, download this issue below or click
here to register with your account number.