Split-Molded Urethane Sprockets
Plan Tech uses a split-mold method instead of injection molding to make cast polyurethane drive and gear sprockets, pads and more. The result is a superior product with a process that can be used for custom parts, as well as production runs for agriculture and other industries.
“Most polyurethane products today are injection molded,” says Kevin Healy, Plan Tech. “We use a 2-part cured system that produces parts that are twice as good as injection molding in terms of tensile strength, rebound, compression, etc.”
Plan Tech starts out by making compression molds for each side, creating mirror images of up to 9 parts per mold. Technicians then hand mix each batch of polyurethane and pour it into the molds.
Once the materials have cured, pairs of parts are put together under 50 tons of pressure.
“The pressure chemically bonds the two together, and it then cures as one form,” says Healy. “The process is economical, too. A sprocket that we make and sell for $10 originally sold for $25.”
The company has perfected the process, enabling the production of thousands of parts of different sizes each month. Each is perfect and requires no machining. However the process also lends itself to smaller, even individual runs. Custom sprockets can be produced as small as 1/2 in. or as large as 4 ft. in dia.
Existing sprockets with a hub or core that are still in good shape can be recoated, cleaned and refurbished with a new urethane coating. Gear sprockets can also be reverse-engineered or redesigned with a new profile or detail added. In high stress applications, a steel core can be added to increase load capacity.
“If you have a part that is already in circulation, we can engineer, mold and make it in your preferred color and hardness,” says Healy.
Not all the jobs require the double cast molding process. Parts can also be machined out of urethane.
“We do a lot of parts for antique farm equipment,” adds Healy.
A recent custom job was a 50-year old track tractor drive sprocket. Previous coatings had worn away to the original steel core. After cleaning the wheel cores, marks were made for machining. A low cost mold was made to over pour the wheel into a solid blank disk, which was then machined to the exact shape needed.
Contact: FARM SHOW Followup, Plan Tech, 7031 Shaker Rd., Loudon, N.H. 03307 (ph 877 349-0620; info@plantech.com; www.plantech.com).
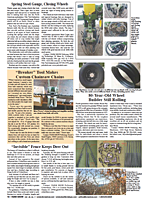
Click here to download page story appeared in.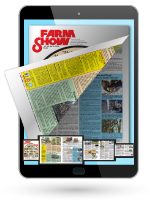
Click here to read entire issue
Split-Molded Urethane Sprockets FARM SHOP Parts Plan Tech uses a split-mold method instead of injection molding to make cast polyurethane drive and gear sprockets pads and more The result is a superior product with a process that can be used for custom parts as well as production runs for agriculture and other industries “Most polyurethane products today are injection molded ” says Kevin Healy Plan Tech “We use a 2-part cured system that produces parts that are twice as good as injection molding in terms of tensile strength rebound compression etc ” Plan Tech starts out by making compression molds for each side creating mirror images of up to 9 parts per mold Technicians then hand mix each batch of polyurethane and pour it into the molds Once the materials have cured pairs of parts are put together under 50 tons of pressure “The pressure chemically bonds the two together and it then cures as one form ” says Healy “The process is economical too A sprocket that we make and sell for $10 originally sold for $25 ” The company has perfected the process enabling the production of thousands of parts of different sizes each month Each is perfect and requires no machining However the process also lends itself to smaller even individual runs Custom sprockets can be produced as small as 1/2 in or as large as 4 ft in dia Existing sprockets with a hub or core that are still in good shape can be recoated cleaned and refurbished with a new urethane coating Gear sprockets can also be reverse-engineered or redesigned with a new profile or detail added In high stress applications a steel core can be added to increase load capacity “If you have a part that is already in circulation we can engineer mold and make it in your preferred color and hardness ” says Healy Not all the jobs require the double cast molding process Parts can also be machined out of urethane “We do a lot of parts for antique farm equipment ” adds Healy A recent custom job was a 50-year old track tractor drive sprocket Previous coatings had worn away to the original steel core After cleaning the wheel cores marks were made for machining A low cost mold was made to over pour the wheel into a solid blank disk which was then machined to the exact shape needed Contact: FARM SHOW Followup Plan Tech 7031 Shaker Rd Loudon N H 03307 ph 877 349-0620; info@plantech com; www plantech com
To read the rest of this story, download this issue below or click
here to register with your account number.