Converted Forage Wagons Dump Into Bunker Silos
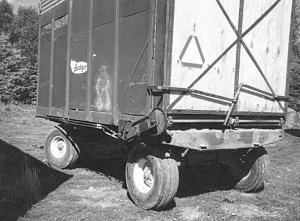 ✖  |
When Duane Gran, St. Peter, Minn., switched from upright silos to bunker silos, he modified a pair of front-unloading for-age wagons by converting them from ptooperated, front-unloading models to hydraulic-driven, rear-unloading models.
"They unload a lot faster now and I saved the cost of new rear-unloading wagons. My wagons were already about 20 years old and the front-unloading conveyors were worn out. By converting them to rear-unload I expect they'll last at least another 10 years. I spent only about $800 to modify each wagon," says Gran.
He cut off the front end of each wagon and removed the conveyor and beaters, then used a skidsteer loader to lift the box up and turn it around. He made a plywood door on back (where the front-unloading conveyor had been) that's hinged on top and supported by an angle iron frame. The entire door is reinforced by lengths of strap iron.
An orbit motor is used to rear-unload the wagon off the tractor hydraulics. Gran mounted a large sprocket onto a shaft that drives the floor apron chain and chain-drives it with the orbit motor.
"It takes only about two minutes to dump a full load," says Gran. "We mounted automatic hitches on the chopper and both wagons so that the tractor drivers never have to get out of their cabs. It speeds things up.
"I think this idea would work with any wagon brand. I paid $300 for the orbit motor. It's probably bigger than I needed, but I didn't know how much power it would take to unload the wagon and I wanted to make sure the motor wasn't underpowered.
"My son Dave did most of the work."
Contact: FARM SHOW Followup, Duane Gran, Rt. 3, Box 63, St. Peter, Minn. 56082 (ph 507 246-5357).
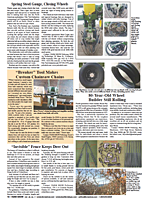
Click here to download page story appeared in.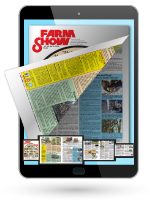
Click here to read entire issue
Converted Forage Wagons Dump Into Bunker Silos CROP STORAGE Bunk Silos 21-2-38 When Duane Gran, St. Peter, Minn., switched from upright silos to bunker silos, he modified a pair of front-unloading for-age wagons by converting them from ptooperated, front-unloading models to hydraulic-driven, rear-unloading models.
"They unload a lot faster now and I saved the cost of new rear-unloading wagons. My wagons were already about 20 years old and the front-unloading conveyors were worn out. By converting them to rear-unload I expect they'll last at least another 10 years. I spent only about $800 to modify each wagon," says Gran.
He cut off the front end of each wagon and removed the conveyor and beaters, then used a skidsteer loader to lift the box up and turn it around. He made a plywood door on back (where the front-unloading conveyor had been) that's hinged on top and supported by an angle iron frame. The entire door is reinforced by lengths of strap iron.
An orbit motor is used to rear-unload the wagon off the tractor hydraulics. Gran mounted a large sprocket onto a shaft that drives the floor apron chain and chain-drives it with the orbit motor.
"It takes only about two minutes to dump a full load," says Gran. "We mounted automatic hitches on the chopper and both wagons so that the tractor drivers never have to get out of their cabs. It speeds things up.
"I think this idea would work with any wagon brand. I paid $300 for the orbit motor. It's probably bigger than I needed, but I didn't know how much power it would take to unload the wagon and I wanted to make sure the motor wasn't underpowered.
"My son Dave did most of the work."
Contact: FARM SHOW Followup, Duane Gran, Rt. 3, Box 63, St. Peter, Minn. 56082 (ph 507 246-5357).
To read the rest of this story, download this issue below or click
here to register with your account number.