You have reached your limit of 3 free stories. A story preview is shown instead.
To view more stories
(If your subscription is current,
click here to Login or Register.)
Home-Built Forage Chopper
"Each one cuts 60,000 tons of silage a sea-son and they've been virtually trouble-free from day one," says Ray Froese about three low-maintenance, high-performance forage harvesters he and his brother, Larry, built.
The Inman, Kan., custom cutters built their own forage harvesters to get away from some of the sho
..........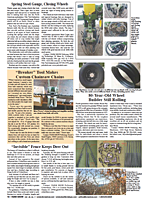
You must sign in, subscribe or renew to see the page.
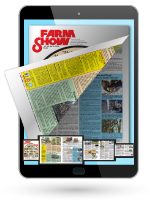
You must sign in, subscribe or renew to see the flip-book
Home-Built Forage Chopper FORAGE HARVESTERS Forage Harvesters (31F) 21-2-40 "Each one cuts 60,000 tons of silage a sea-son and they've been virtually trouble-free from day one," says Ray Froese about three low-maintenance, high-performance forage harvesters he and his brother, Larry, built.
The Inman, Kan., custom cutters built their own forage harvesters to get away from some of the shortcomings they observed in new sophisticated factory machines.
"One reason we build our own is the astronomical cost of new machines. Some go for as much as $250,000," Ray says. "An-other is that there seemed to be excessive downtime with new equipment. Downtime can cost you plenty when you've got only a three-month window to do your entire season's cutting. Plus, parts are very expensive on new, factory-built machines. Our machine is designed so we can replace parts in half the time at half the cost."
The men used essentially the same design for all three machines. The main frame is made out of 4 by 10-in. tubing. It's fitted with the front axle off an N7 Gleaner combine and the rear axle off a 1680 IH combine. Front drive wheels are off a Deere tractor and are fitted with 20.8 by 38-in tires to adapt to 30, 36 and 40-in. rows. Rear tires are 16.9 by 24-in.
Power is supplied by a 6-cyl. 450 hp 3406B Caterpillar engine out of a Peterbilt semi. It mounts sideways between the cab and radiator."By mounting it crossways, we didn't have to change direction of the power drive with a gearbox which is what adds a lot of expense and complexity to some ma-chines," Froese notes.
The cutterknives and blower are belt-driven by an industrial 300-in. long belt and special pulley drive. "If there's ever any downtime, it'll only be to replace the one belt," Ray says. "It doesn't take much power to belt-drive the cutterbars and blower."
Each machine is fitted with a 6-row Kemper head powered by a 20 gpm Sundstrand hydraulic pump. The system is designed with a series of bypasses to avoid damage to the head in case of trouble.
A huge, 50-gal. capacity radiator mounts on back of the machine. The 6-ft. tall, 5 1/ 2-ft. wide, 6-in. thick radiator came out of an 800 hp Kenworth coal truck and is equipped with a hydraulically driven 36-in. dia. fan for blowing air out of the rear of the machine, moving heat and noise away from the driver.
"On cool mornings we run the fan real slow and turn up the speed as the day heats up," says Ray. "When leaves or other crop material plugs up screens or the radiator, we flip a switch in the cab to reverse direction of the fan and blow them clean."
The machine is equipped with a 34-in. wide, 24-in. dia. cutter drum fitted with 60 Deere knives from a 6810 forage harvester. It has a home-built 12-ft. long, 12-in. spout fitted with easy-replace, bolt-on plastic liners. "It's perfectly arched so silage comes out smoothly and doesn't wear on the liners as much," Ray says. It also rotates 280 degrees to increase ease of truck filling, he adds. The cab is off a Gleaner L combine. It rests on rubber mounts.
The Froese brothers say they've got about $130,000 invested in each machine. Contact: FARM SHOW Followup, Froese Brothers, Box 139, Inman, Kan. 67546 (ph 316 585-6478 or 2590).
To read the rest of this story, download this issue below or click
here to register with your account number.