You have reached your limit of 3 free stories. A story preview is shown instead.
To view more stories
(If your subscription is current,
click here to Login or Register.)
He Turned His Garden Tractor Into A Mini Bulldozer
A "mini" bulldozer made from a junked out 1969 International Cub Cadet lawn and garden tractor lets William "Crank" Cranford, Indian Head, Md., push snow and gravel along his steep driveway as well as pull out small tree stumps.
The "mini" bulldozer, which Cranford built two years ago, is 40 in. wide and equippe
..........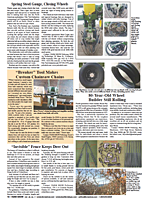
You must sign in, subscribe or renew to see the page.
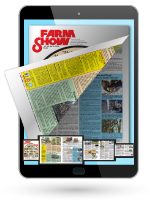
You must sign in, subscribe or renew to see the flip-book
He turned his garden tractor into a mini bulldozer FARM HOME Miscellaneous 13-3-10 A "mini" bulldozer made from a junked out 1969 International Cub Cadet lawn and garden tractor lets William "Crank" Cranford, Indian Head, Md., push snow and gravel along his steep driveway as well as pull out small tree stumps.
The "mini" bulldozer, which Cranford built two years ago, is 40 in. wide and equipped with an 18-in. high, 42-in. wide blade. Its steel tracks measure 6 in. wide, 13 1/2 in. high and 54 1/2 in. long.
"It outperforms any of my wheeled Cub Cadets. Improved traction is the key," says Cranford, a retired machinist and collector of Cub Cadets. "On my steep driveway none of my Cadets can push much snow or gravel. The tires spin, even when they're equipped with chains. However, the bulldozer's tracks don't slip at all. The only drawback is that if I'm not careful the cleats dig up my lawn when I turn."
Cranford discarded the Cub Cadet's seat, rear fenders, wheels, front axle, steering wheel, steering column and tie rods, keeping the rear axle, hydrostatic trans-mission, gas tank and starter. He installed a new front axle made from 1-in. cold rolled steel. Then he used two 54 1/2-in. long, 4-in. wide channel irons to build an undercarriage for the Cub Cadet, welding the rails together with 1/4-in. flat iron and 1-in. dia. pipe. Inside each rail he in-stalled five idler wheels to support the tracks. Then he lowered the Cub Cadet chassis into the undercarriage and bolted them together. To drive the tracks, he installed two sprockets side-by-side on the end of each rear axle. He bolted the larger of the two sprockets on the outside of the flange and bolted the smaller sprocket on the inside of the flange, then installed chain tighteners. He installed another sprocket, removed from a Harley Davidson motorcycle, to apply the disc brakes. Cranford steers the bulldozer by pulling forward or backward on two levers which control the hydraulic disc brakes. Cranford purchased a set of commercial tracks._ Using lengths of threaded pipe, he made a tool to draw and pin the track ends together. Next Cranford installed a new 12 hp short block Kohler engine and a new seat removed from a later model Cub Cadet.
Cranford built his own stump puller by welding together two old split truck rims to form a drum. He welded one end of a 5-ft. long, 21/2-in. dia. pipe to the middle of the drum, bracing the pipe by welding strap metal between it and the drum. A 3/ 8-in. cable runs from the pipe to a chain fastened onto the bulldozer's rear hitch. The cable runs through a set of double blocks which provide additional lever-age. To pull a stump, Cranford places the drum, with the pipe standing straight up, against the stump and wraps a chain around its back side, then pulls with the bull-dozer.
"If I built another dozer, I'd install a gear transmission with a creeper gear to cut speeds in half," says Cranford, noting that the rig's hydrostatic transmission wasn't designed for heavy pulling. He says he spent about $3,000 to build the dozer.
Contact: FARM SHOW Followup, William "Crank" Cranford, Rt. 2, Box 35, Indian Head, Md. 20640 (ph 301743-7718).
To read the rest of this story, download this issue below or click
here to register with your account number.