You have reached your limit of 3 free stories. A story preview is shown instead.
To view more stories
(If your subscription is current,
click here to Login or Register.)
Big Tractor Power With A Low Price Tag
Big tractors cost lots of money, unless you build your own like G. R. Rasmussen and his son, Brian, did in the workshop on their farm near Standard, Alberta, Canada. Their homemade 135 hp tractor started as a Mack truck and the rear end from a Euclid machine found in a scrap yard. It took one winter and about $3,500 to
..........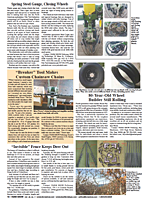
You must sign in, subscribe or renew to see the page.
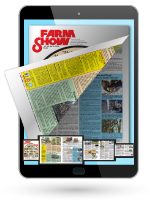
You must sign in, subscribe or renew to see the flip-book
Homemade Tractor From A Mack Truck TRACTORS Conversions 6-2-9 Big tractors cost lots of money, unless you build your own like G. R. Rasmussen and his son, Brian, did in the workshop on their farm near Standard, Alberta, Canada. Their homemade 135 hp tractor started as a Mack truck and the rear end from a Euclid machine found in a scrap yard. It took one winter and about $3,500 to put the tractor together. "We've been using it for ten years and it's still going strong," says Brian.
The Rasmussens particularly liked the big displacement (673 cubic inches) and slow speed (1600-1700 rpm) of the Mack engine. That power, plus a 15-speed transmission with 10 speeds slower than 10 mph, lets them pull a 36 ft. hoe drill with fertilizer attachment, or a 36 ft. chisel plow and smoothing harrow. Top speed is about 20 mph, but their normal field speed is about 4 to 6.5 mph, says Brian. So, it's easy to match power to the implement and field conditions.
The frame of the Mack truck was cut off just back of the cab and welded to the underside of the Euclid axle. The frame was reinforced with extra beams and the driveshaft shortened and coupled to the Euclid differential. However, the truck front suspension and steering system remained unchanged, with the short wheelbase permitting sharp, quick turns. An extra brake pedal was added to provide individual braking of rear wheels for easier turning.
New dual wheel rims and dual 18.4-38 tires added to the tractor's cost, but were worth it, according to the Rasmussens. The rear axle had a positive traction differential when they bought it. Concerned that this might restrict maneuverability, the Rasmussens installed a new "spider" and have no differential lock now. However, this has not been a problem, according to Brian, who notes that "we've had very little problem with the tractor ever getting stuck."
"The combination of truck front suspension, the truck seat, and the mid-tractor operator location provide a very smooth ride. The cab is cleaner and quieter than the cabs on many tractors. One reason for the lower noise level is the slower engine speed, compared to most current tractors," Brian points out. The original sealed beam headlights were retained and sealed beam work lights were mounted on the back side of the cab. An old power steering pump, driven from the front of the engine, provides hydraulic power for implement control. It's a bit slow, admits Brian, but it was economical and he says the system doesn't need high capacity for their work. Two remote valves are located in the cab, and a used air tank on the front bumper is the oil reservoir.
To prevent kinking or damaging hydraulic hoses between the tractor and implement, the hoses and couplers are supported on a vertical pipe bracket welded to the swinging drawbar. This keeps hoses more in line with the implement tongue and requires less slack than if the couplers and hoses were mounted on the axle. The drawbar was made from the 2 3/4-in. square steel frame of a Minneapolis-Moline one-way tiller.
Would they build another tractor like this one?
"We've considered it," says Brian, noting that these are the components and features he and his dad would look for or want to include in the next model they build:
"First of all, we'd look for a big, slow-speed 6-cylinder engine. We feel that newer truck cabs are higher and most have larger windows, so visibility would be better. The rear end might come from a junked tractor, an earth mover, or perhaps even a æretired' 4-wheel drive. A new 2-wheel drive tractor with 135 hp costs about $60,000. I'm sure we could build one for a lot less than that."
For more information, contact: FARM SHOW Followup, Brian Rasmussen, Box 363, Standard, Alberta TOJ 3G0 (ph 403 644-3800).
To read the rest of this story, download this issue below or click
here to register with your account number.