Rebuilt Spreader Works "Better Than New"
When the apron drive on a customer's Balzer manure spreader wore out, repair shop owner Terry Therkilsen, Comfrey, Minn., converted it to hydraulic drive, providing variable speed control of the apron right from the tractor cab. He also replaced the front and rusted-out sides of the 440 bu. spreader, as well as the floor.
The spreaders apron and beaters were originally chain-driven off the pto through a gear reduction box. Therkilsen connected a 30 hp Charlynn high pressure, high torque hydraulic motor to the input shaft on the gear reduction box. Motor speed is regulated by a flow control valve from the tractor cab. The beaters are still pto-driven.
The front of the spreader originally came straight down about half way to the floor, then swept back at a 45 degree angle to keep manure from falling off the front of the apron. However, the shallow angle also prevented wet manure from sliding down onto the apron. To solve the problem he used sheet metal to build a new front side that goes back at a steeper angle. The wooden floor was worn out and broken in places so he replaced it with a new plywood one.
"Converting the spreader to hydraulic drive was more expensive than rebuilding the existing drive system, but it improved performance of the spreader because of the variable speed drive," says Therkilsen. "Many farmers want to keep their old spreader instead of spending the money for a new one. I've rebuilt 10 or 12 other Balzer spreaders in the past few years. Most of them are 15 to 20 years old and range in capacity from 300 to 500 bu. It costs about $800 to $1,200 to rebuild most spreaders and up to $2,000 for the bigger ones. The company now offers a hydraulic drive option that can be retrofitted to existing spreaders."
Contact: FARM SHOW Followup, Terry Therkilsen, Progressive Designs, Rt. 1, Box 146, Comfrey, Minn. 56019 (ph 507 723-6130).
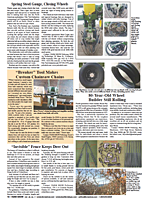
Click here to download page story appeared in.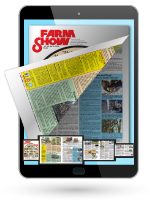
Click here to read entire issue
Rebuilt Spreader Works "Better Than New" MANURE HANDLING Equipment 21-5-9 When the apron drive on a customer's Balzer manure spreader wore out, repair shop owner Terry Therkilsen, Comfrey, Minn., converted it to hydraulic drive, providing variable speed control of the apron right from the tractor cab. He also replaced the front and rusted-out sides of the 440 bu. spreader, as well as the floor.
The spreaders apron and beaters were originally chain-driven off the pto through a gear reduction box. Therkilsen connected a 30 hp Charlynn high pressure, high torque hydraulic motor to the input shaft on the gear reduction box. Motor speed is regulated by a flow control valve from the tractor cab. The beaters are still pto-driven.
The front of the spreader originally came straight down about half way to the floor, then swept back at a 45 degree angle to keep manure from falling off the front of the apron. However, the shallow angle also prevented wet manure from sliding down onto the apron. To solve the problem he used sheet metal to build a new front side that goes back at a steeper angle. The wooden floor was worn out and broken in places so he replaced it with a new plywood one.
"Converting the spreader to hydraulic drive was more expensive than rebuilding the existing drive system, but it improved performance of the spreader because of the variable speed drive," says Therkilsen. "Many farmers want to keep their old spreader instead of spending the money for a new one. I've rebuilt 10 or 12 other Balzer spreaders in the past few years. Most of them are 15 to 20 years old and range in capacity from 300 to 500 bu. It costs about $800 to $1,200 to rebuild most spreaders and up to $2,000 for the bigger ones. The company now offers a hydraulic drive option that can be retrofitted to existing spreaders."
Contact: FARM SHOW Followup, Terry Therkilsen, Progressive Designs, Rt. 1, Box 146, Comfrey, Minn. 56019 (ph 507 723-6130).
To read the rest of this story, download this issue below or click
here to register with your account number.