You have reached your limit of 3 free stories. A story preview is shown instead.
To view more stories
(If your subscription is current,
click here to Login or Register.)
They Build Their Own Tillage Rigs
"If I can't buy the tillage equipment I need I either build my own or rebuild existing equipment. The result is tremendous cost savings," says Leslie Johnston who, along with sons Danny and Doyle, put together three home-built tillage rigs.
The tillage rigs include a 28-ft. wide disk harrow with a 29-ft., hydrau
..........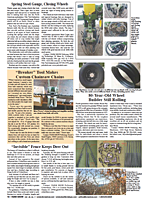
You must sign in, subscribe or renew to see the page.
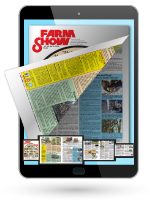
You must sign in, subscribe or renew to see the flip-book
They Build Their Own Tillage Rigs TILLAGE EUIPMENT Disks (18) 22-1-12 "If I can't buy the tillage equipment I need I either build my own or rebuild existing equipment. The result is tremendous cost savings," says Leslie Johnston who, along with sons Danny and Doyle, put together three home-built tillage rigs.
The tillage rigs include a 28-ft. wide disk harrow with a 29-ft., hydraulic-fold roller on back; a 27-ft. field cultivator pulling a 500-gal. stainless steel nurse tank; and a 20-ft. drill equipped with a spring tooth cultivator and roller on front.
"We plant 500 to 600 acres of soybeans each year and have used these rigs for 5 years. They each do several jobs in one pass which saves a lot of time and fuel," says Johnston.
Disk-Roller: He built the roller out of a used 15-ft. Deere Culti-Mulcher. "The roller's tongue is so heavy I had to make a dolly to support its weight. The dolly hitch attaches to the disk's front gang and is equipped with crazy wheels that came off a Hi-Boy 4-wheeled sprayer. I used channel iron to build the dolly. Hydraulic hoses run directly from the disk to the cylinders on the roller so that when I turn the disk and roller both raise at the same time. The roller wings fold straight up for transport. The roller breaks up clods without compacting the soil and makes a beautiful seedbed. We some-times pull it behind the field cultivator.
"We use a 340 hp articulated tractor to pull this combination."
Field Cultivator & Spray Tank: Johnston used 3-in. sq. steel tubing to build the 27-ft. field cultivator which is used to incorporate chemicals. A pto-operated pump applies chemicals through a boom mounted on front of the cultivator. A Remlinger 3-bar harrow mounts on back. "A comparable size Deere field cultivator sells for about $18,000," says Johnston. "The cultivator has six rows of teeth for excellent trash clearance. Most conventional field cultivators have only four rows of teeth. The 27-in. long vibrating shanks really shake the dirt and mix the soil well. We set the shanks to run about 2 in. deep and go 7 to 8 mph.
"The tank carrier frame is built from 6 in. sq. steel and is strong enough to support a 1,000-gal. tank. It mounts on a pair of dual crazy wheels on back and single solid wheels in front. I used 2 1/2-in. dia. steel pipe to build the tank carrier's 20-ft. tongue. The tongue is long enough that when I turn, the field cultivator and harrow swing under it without interference. By building the tank carrier myself I saved about 90 percent of the cost of a new commercial rig. I use a Case-IH 1586 2-WD, 225 hp tractor or an Allis-Chalmers 7080 to pull this combination."
Drill Cultivator Combo: The 20-ft. spring tooth cultivator, roller, and 3-pt. Great Plains drill all mount on a carrier that hooks up to the tractor drawbar. The carrier is sup-ported by a pair of 4-ft. high wheels and an 8-ton axle and spindles off a big fertilizer sprayer. The cultivator is equipped with 15-in. long S-tines that level the soil, wiping out wheel tracks. "I spent about $7,000 to build the cultivator. A comparable commerical unit would sell for about $18,000," notes Johnston.
There are two gauge wheels on front of the cultivator, and the roller itself serves as a gauge wheel for the back of the cultivator. Johnston made the roller by converting a Deere Culti-mulcher originally equipped with two 10-ft. wide sections, one in front of the other. He removed both rollers and mounted them side by side, then used sq. steel tubing and 6 bearings to make an axle. "We use a Case 1370 2-WD tractor equipped with duals wheels to pull this combination," says Johnston.
Contact: FARM SHOW Followup, Leslie Johnston, RR 1, Box 16, Mason, Ill. 62443 (ph 618 238-4318).
To read the rest of this story, download this issue below or click
here to register with your account number.