You have reached your limit of 3 free stories. A story preview is shown instead.
To view more stories
(If your subscription is current,
click here to Login or Register.)
He Built His Own Bi-Fold Doors
When Nebraska farmer Steve Hietbrink tore down a pair of 40 by 90-ft. chicken houses, he saved the aluminum roofing and all salvagable wood to build a 60-ft. wide, 104-ft. long machine shed and shop. In the process, he designed and built a pair of 16-ft. high bi-fold doors that would have cost thou-sands if he had boug
..........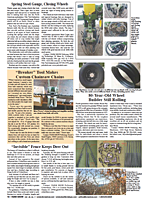
You must sign in, subscribe or renew to see the page.
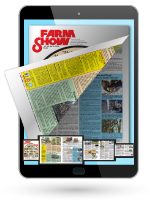
You must sign in, subscribe or renew to see the flip-book
He Built His Own Bi-Fold Doors BUILDINGS Accessories 22-1-32 When Nebraska farmer Steve Hietbrink tore down a pair of 40 by 90-ft. chicken houses, he saved the aluminum roofing and all salvagable wood to build a 60-ft. wide, 104-ft. long machine shed and shop. In the process, he designed and built a pair of 16-ft. high bi-fold doors that would have cost thou-sands if he had bought it new.
"They work as well as any doors on the market. A lot of people come by to look at them," says Hietbrink. "I saved about $5,000 by putting up the shed myself, and I saved about $5,000 on each door."
Half the shed is used as a shop and has a cement floor. The other half is used to store machinery and has a dirt floor. Hietbrink uses a roll-down curtain to separate the two areas. He used aluminum roofing left over from the chicken houses to build the shed's side walls. The roof was built from new material. He also bought new 60-ft. wide clear span roof trusses.
A 30-ft. wide bifold door is built into one end of the shed, and a 24-ft. wide door is on one side. He used 2-in. sq. steel tubing to build frames for the doors.
Hietbrink opens and closes the doors with a two-way switch. An electric motor is used to power a worm drive gearbox, which winches in cables wrapped around a pipe along the bottom of each door. An electric contact system is used to reverse the motor, resulting in "power up, power down" that eliminates the need for a brake system to keep the door from "creeping" down after it's opened. Rollers salvaged from railroad cargo cars ride up and down angle iron tracks at the outside edges of the door.
Contact: FARM SHOW Followup, Steve Hietbrink, Box 88L, Firth, Neb. 68358 (ph 402 791-5777).
To read the rest of this story, download this issue below or click
here to register with your account number.