You have reached your limit of 3 free stories. A story preview is shown instead.
To view more stories
(If your subscription is current,
click here to Login or Register.)
High Volume Air Compressor Built From Old Diesel Tractor Engine
"We needed a high volume air compressor to blow out irrigation lines in the fall but we couldn't justify the $15,000 to $20,000 price tag on a big industrial compressor," says Glen Goby who built a high capacity air compressor using an old diesel tractor engine.
"I don't know exactly what the capacity of it is,"
..........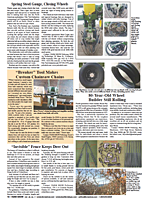
You must sign in, subscribe or renew to see the page.
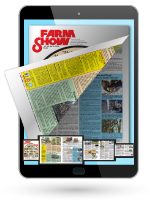
You must sign in, subscribe or renew to see the flip-book
High Volume Air Compressor Built From Old Diesel Tractor Engine ENGINES Engines 20-3-10 "We needed a high volume air compressor to blow out irrigation lines in the fall but we couldn't justify the $15,000 to $20,000 price tag on a big industrial compressor," says Glen Goby who built a high capacity air compressor using an old diesel tractor engine.
"I don't know exactly what the capacity of it is," says the Avonlea, Sask., farmer, "but we can blow out a half mile of 8-in. dia. line in less than 15 minutes running it at about 900 rpm's."
Goby used a 350 cu. in. engine out of late 1940's WD9 IHC tractor he bought from a neighbor. It mounts on a two-wheel trailer made from a 1/2-ton pickup axle.
"We installed commercial air compressor intake valves on the engine," he says. "Then we took the injectors out and fitted the ports with regular air compressor valves so that the injector ports actually became the exhaust valves. The engine sucks air in and blows it out on each stroke."
He used the tractor's original air cleaner on the intake valves and filled the cooling system with oil to dissipate heat. A 2 in. dia. pipe carries oil from the top radiator hose connection to the botom. The pipe is open at the top to allow for expansion.
The engine mounts on the trailer with the flywheel side facing forward so it can be direct-driven off a tractor's pto shaft. Goby had to make a shaft that comes off the flywheel's pilot bearing. He bolted a plate to the flywheel to help center the shaft. He powers the home-built compressor with a 110 hp tractor.
Out-of-pocket expense was $750.
Contact: FARM SHOW Followup, Glen Goby, Box 117, Avonlea, Sask., Canada SOH OCO (ph 306 868-4424).
To read the rest of this story, download this issue below or click
here to register with your account number.