He Built His Own Pto-Driven Air Compressor
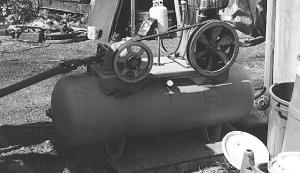 ✖  |
Jack Dyck, Richmond, B.C.: "I built my own pto-driven air compressor by mounting a right angle gearbox and pulley unit - salvaged from an old tractor- on a steel bracket that I bolted onto a 200-gal. air tank. I also mounted a used compressor equipped with its own pulley on the bracket. I use a tractor to pto-drive the gearbox which belt-drives the compressor. The compressor blows air through a copper tube that goes through the bracket and into the tank. The original pulley on the gearbox was designed for a flat belt. I replaced it with a bigger 2-groove pulley, using an adapter to install it.
"I work part time for a construction business and got the idea while working at a place that had no electricity. I was given the compressor and found the tank alongside a road. I made an adjuster that lets me move the bracket back and forth to tighten the belt.
"I also made my own pressure washer that's powered by the engine off a 1962 Volkswagen Beetle car. I removed the clutch plate from the flywheel and filled in the center of the clutch with a small steel plate, then drilled holes into the plate and bolted on a 3-groove pulley. The pulley, covered for safety, belt-drives a Giant pump that I bolted onto a steel bracket. I bolted half of a VW transmission case to the engine block (the early VW transmissions were built in two pieces) and bolted an 8-in. channel iron bracket onto the transmission in order to mount the pump. Water travels from the pump through steel hydraulic hoses and into a wand (not shown). I knocked the valves out of the connectors on the hoses so that they're totally open.
"The original VW fan housing is still used to cool the engine. I didn't change anything on the housing except to close some ducts in order to get more air to the engine. I mounted a pair of switches on the housing. One is the ignition switch (the transmission contains the engine's starter mounting) and the other activates an automatic throttle that I made. The throttle is a flow switch that's activated by flowing water - it closes a relay which energizes an electromagnet on the throttle. It al-ways keeps the engine running at idle until I pull a trigger on the wand - then it will rev up the engine to its pre-set maximum. As soon as I let go of the throttle switch the engine returns to idle.
"The pump bracket has slotted holes for adjusting belt tension. I just loosen a bolt to adjust the tension.
"The fuel tank is from an outboard motor. I use an automotive electric fuel pump to supply the carburetor with fuel. The pump is wired into the ignition switch so that when-ever the ignition is on, the pump is working.
"I'm semi-retired but have started a pressure washing business. I use my homemade pressure washer to clean houses, driveways, sidewalks, etc. I even use it to wash restaurants. It mounts in the back of my pickup."
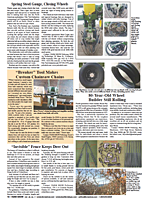
Click here to download page story appeared in.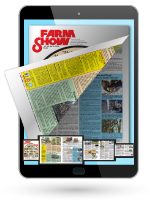
Click here to read entire issue
He Built His Own Pto-Driven Air Compressor FARM SHOP Tools 22-3-30 Jack Dyck, Richmond, B.C.: "I built my own pto-driven air compressor by mounting a right angle gearbox and pulley unit - salvaged from an old tractor- on a steel bracket that I bolted onto a 200-gal. air tank. I also mounted a used compressor equipped with its own pulley on the bracket. I use a tractor to pto-drive the gearbox which belt-drives the compressor. The compressor blows air through a copper tube that goes through the bracket and into the tank. The original pulley on the gearbox was designed for a flat belt. I replaced it with a bigger 2-groove pulley, using an adapter to install it.
"I work part time for a construction business and got the idea while working at a place that had no electricity. I was given the compressor and found the tank alongside a road. I made an adjuster that lets me move the bracket back and forth to tighten the belt.
"I also made my own pressure washer that's powered by the engine off a 1962 Volkswagen Beetle car. I removed the clutch plate from the flywheel and filled in the center of the clutch with a small steel plate, then drilled holes into the plate and bolted on a 3-groove pulley. The pulley, covered for safety, belt-drives a Giant pump that I bolted onto a steel bracket. I bolted half of a VW transmission case to the engine block (the early VW transmissions were built in two pieces) and bolted an 8-in. channel iron bracket onto the transmission in order to mount the pump. Water travels from the pump through steel hydraulic hoses and into a wand (not shown). I knocked the valves out of the connectors on the hoses so that they're totally open.
"The original VW fan housing is still used to cool the engine. I didn't change anything on the housing except to close some ducts in order to get more air to the engine. I mounted a pair of switches on the housing. One is the ignition switch (the transmission contains the engine's starter mounting) and the other activates an automatic throttle that I made. The throttle is a flow switch that's activated by flowing water - it closes a relay which energizes an electromagnet on the throttle. It al-ways keeps the engine running at idle until I pull a trigger on the wand - then it will rev up the engine to its pre-set maximum. As soon as I let go of the throttle switch the engine returns to idle.
"The pump bracket has slotted holes for adjusting belt tension. I just loosen a bolt to adjust the tension.
"The fuel tank is from an outboard motor. I use an automotive electric fuel pump to supply the carburetor with fuel. The pump is wired into the ignition switch so that when-ever the ignition is on, the pump is working.
"I'm semi-retired but have started a pressure washing business. I use my homemade pressure washer to clean houses, driveways, sidewalks, etc. I even use it to wash restaurants. It mounts in the back of my pickup."
To read the rest of this story, download this issue below or click
here to register with your account number.