You have reached your limit of 3 free stories. A story preview is shown instead.
To view more stories
(If your subscription is current,
click here to Login or Register.)
"John Holland Swather"
"I raise alfalfa hay for sale at a feed store so producing high-quality hay is a must," says Dave Miller who built what he calls a "John Holland" swather using the powertrain off a Deere 2280 swather and the header off a 488 New Holland pull-type haybine. The goal was to achieve the speediest drying time in order to pr
..........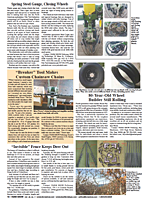
You must sign in, subscribe or renew to see the page.
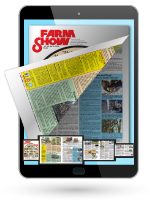
You must sign in, subscribe or renew to see the flip-book
"John Holland Swather" SWATHERS Swathers 22-4-25 "I raise alfalfa hay for sale at a feed store so producing high-quality hay is a must," says Dave Miller who built what he calls a "John Holland" swather using the powertrain off a Deere 2280 swather and the header off a 488 New Holland pull-type haybine. The goal was to achieve the speediest drying time in order to produce the highest-quality, best-looking product.
The Oregon farmer previously used two 1960's New Holland 1469's with narrow 9-ft. wide headers and full width rubber conditioning rolls which put hay in completely flat 7 1/2-ft. wide windrows. Two swaths, equivalent to an 18-ft. swath, were then twin raked together ahead of Miller's balers.
However, after using the pair of haybines for more than 20 years, he found parts next to impossible to get. Plus, the old haybines had several drawbacks - gas engines, planetary drives, high-maintenance driveshafts, and no air conditioning.
"I still wanted the narrow swath and the wide conditioner, but no one builds a self-propelled machine that size," Miller says. He started with a 9-ft. pull-type New Holland header, discarding the running gear. "With a little measuring, I found that a Deere 2280 series swather powertrain would track behind the header if we changed to smaller wheels fitted with 12.4 by 18-in. turf tires," he says.
A new set of header lift arms was fabricated out of mild steel and attached to the existing lift points on both the header and powertrain. Existing Deere hydraulic lift cylinders were used, while counter balance springs from the New Holland machine pro-vide "float" for the header.
"I removed the pulleys, belt, and header drive from the Deere and installed an industrial 30 gpm hydraulic pump behind the gear box using the Deere driveshaft, which I shortened by half," Miller says.
"The pump is supplied with oil from a 30-gal. reservoir mounted on the right side of the cab and drives a piston-type motor mounted on the header. The system is con-trolled with a ball valve and a bypass line and pressure regulator. When the header is taken out of gear, the conditioner rollers act like a flywheel, so a check valve was necessary to prevent the motor from turning into a pump and reversing oil flow. The return oil is routed through an oil cooler with an electric 12-volt fan mounted behind the cab.
"A dummy shaft was installed in place of the pto gearbox on the header and connects to the hydraulic motor with a high speed roller chain and hardened sprockets. The hydraulic drive absorbs a lot of the shock from the conditioner and makes a smoother running header."
Miller likes the machine's diesel engine, hydrostatic ground drive, air conditioned cab and Deere tractor-style seat. Because of the forward positioning of the header, it also offers the operator a better view of the crop coming through the rolls and the ground be-hind the cutterbar, making it easier to spot any potential plugs.
The only machining required for the project was shortening the gear box drive line and yoke, and the dummy shaft to replace the pto gearbox on the header, says Miller.
"The only minor problem I've noticed is that, because of the smaller tires, you lose a couple mph's from the normal transport speed of 15 mph," he says. "Otherwise, I used the machine last year to make four cuttings on 200 acres and it performed flawlessly."
Out-of-pocket expense was $8,500. Contact: FARM SHOW Followup, Dave Miller, 85090 Winesap Rd., Milton-Freewater, Ore. 97862 (ph 541 938-6253).
To read the rest of this story, download this issue below or click
here to register with your account number.