You have reached your limit of 3 free stories. A story preview is shown instead.
To view more stories
(If your subscription is current,
click here to Login or Register.)
Heavy-Duty Shop-Built Metal Roller
Commercial units are real hard to come by and you have to pay through the nose if you ever find one," says Bruce Barnes about a heavy-duty metal roller he and his employee Chad Burnett built out of components Barnes collected over a period of five or six years. It handles sheet metal up to 8 ft. wide and 1/4-in. thick
..........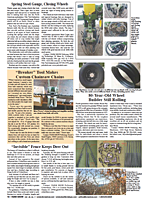
You must sign in, subscribe or renew to see the page.
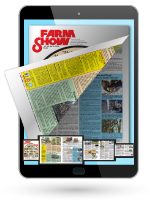
You must sign in, subscribe or renew to see the flip-book
Heavy-Duty Shop-Built Metal Roller FARM SHOP Tools 23-2-39 Commercial units are real hard to come by and you have to pay through the nose if you ever find one," says Bruce Barnes about a heavy-duty metal roller he and his employee Chad Burnett built out of components Barnes collected over a period of five or six years. It handles sheet metal up to 8 ft. wide and 1/4-in. thick and will roll any diameter necessary.
The Girard, Ill., welder has used the machine to roll snow plow blades, grain bin hopper bottoms, auger troughs, replacement buckets for backhoes, and barrels.
It features three solid steel rolls weighing 1,000 lbs. apiece. They're made out of a salvaged industrial size machine bolt cut into three 8-ft. long sections. Originally 6 1/2 in. in dia., the giant threaded bolt sections were turned down flat to exactly 6 in. on Barnes' lathe, which took a month. The rollers mount together in a triangular configuration, held in place by side panels made out of 2 in. solid plate. Four cross-braces made out of 1/2-in. thick pipe hold the unit together.
A 5 hp electric gear reduction motor drives the bottom roller mounted using a double #80 roller chain and sprocket. A 1 hp electric motor at each side of the machine moves the rear roller up and down to vary the finished diameter of the material being rolled. The two motors are wired to run independently or together.
The machine is fitted on the left side with a cam latch made out of pipe to open the side to remove large dia. pieces.
A control panel, also mounted on the left side, swivels to permit operating the machine from the center or off to the side.
Altogether, the roller weighs 5,200 lbs. and stands about 30 in. tall.
"The trickiest part was getting the rollers wired to run independently or together. It took an electrician quite a while to figure that out," Barnes says. "We've used it for several jobs since completing it in January and it works beautifully."
Out-of-pocket expense was $1,500, including $500 in new parts, compared with commercial units that cost $20,000 or more.
Contact: FARM SHOW Followup, Bruce's Welding, 302 S Third, Girard, Ill. 62640 (ph 217 627-2241).
To read the rest of this story, download this issue below or click
here to register with your account number.