You have reached your limit of 3 free stories. A story preview is shown instead.
To view more stories
(If your subscription is current,
click here to Login or Register.)
Old Baler Makes Great Windrow Inverter
"I put up only about 400 tons of hay a year. But my area's pretty wet and it's usually hard to get finished before my hay gets rained on," says Randy Barta who built a windrow inverter out of an old baler. It flips the wind-rows to reduce drying time to three days in-stead of five or six. "It works better than any comm
..........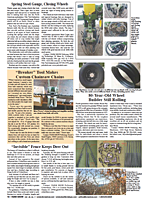
You must sign in, subscribe or renew to see the page.
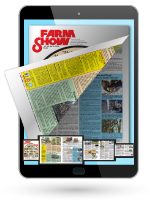
You must sign in, subscribe or renew to see the flip-book
Old Baler Makes Great Windrow Inverter BALERS Balers 22-6-36 "I put up only about 400 tons of hay a year. But my area's pretty wet and it's usually hard to get finished before my hay gets rained on," says Randy Barta who built a windrow inverter out of an old baler. It flips the wind-rows to reduce drying time to three days in-stead of five or six. "It works better than any commercial unit I've ever seen," he says.
The Lewistown, Mont., farmer started with an IH 2400 round baler, stripping it down to the frame and salvaging many parts for the project.
"It's built like a New Holland inverter," Barta says. "The big difference is, when you drive over windrows with my unit at the end of the field it doesn't make such a mess of the hay."
That's because he built the inverter so it pivots up and down on the axle. Two hydraulic cylinders raise the machine and pickup at the same time, providing up to 2 ft. of ground clearance to easily pass over end windrows.
Barta made a horizontal belt out of a 30-in. wide draper belt off an old New Holland windrower. The pickup drops the hay on the belt which then carries it over to an inverter chute made of tin. A 5-in. "elevator" belt mounts between the pickup and the large horizontal belt. "It gives us more lift," says Barta. "We lift the windrow up 12 in. higher than any commercial inverter I've seen, which helps reduce plugging in heavy hay."
To solve the problem of plugging when hay comes around the corner of the horizontal belt onto the outfeed chute, Barta mounted a 1-in. dia. vertical shaft fitted with rake teeth just inside the shield at the corner. He cut slots in the shield so the rake teeth extend through them. The shaft is belt-driven and, as it turns, assists the hay around the corner.
The inverter handles windrows up to 5-ft. wide and is pulled by Barta's Deere 4020, although any 45 hp tractor with hydraulics could be used to pull it, he says.
"Most of the parts I needed for the inverter were extras I removed from the baler when I stripped it down," he says. "The whole project cost me only around $300, compared with $4,000 or more for a commercial model. What's best is, from what I can see, it out-performs commercial models."
Contact: FARM SHOW Followup, Randy Barta, Rt. 1, Box 1854, Lewistown, Mont. 59457 (ph 406 538-7319).
To read the rest of this story, download this issue below or click
here to register with your account number.