SP Forage Harvester Carries "Piggyback" Truck
When Gunther Alexander heads out to the field in his self-propelled forage harvester, he's not surprised when people stop on the road to stare. He knows no one's ever seen a rig quite like his.
The Vauxhall, Alberta, farmer-inventor carries a 3-ton truck on the back of his Deere 5400 harvester. When the truck gets full, he drives it off the 22-ft. deck and heads back to the farm.
The entire rig is 55 ft. long and 16 ft. wide and is equipped with big 30.5 by 32 flotation tires on front (off a Deere 8820 combine) and smaller tires on back. The rear axle is used for steering and there's a 12-ft. hydraulic-operated loading ramp on back.
Alexander blows the haylage into a 2-ft. opening at the back of the truck which has a 20-ft. long, 8-ft. high box. The forage harvester's spout actually extends inside the truck. The box raises hydraulically and dumps its load out through an 8-ft. wide door at the back.
"This setup lets me do the job alone or with one helper, and it eliminates the hassle of filling a truck on-the-go," says Alexander. "I generally use two trucks. An employee drives one truck to town while I fill the other one. Each truck can haul 10 tons of 40 percent moisture haylage.
"I use it on my own farm and I also do custom work for area farmers. Most farmers who chop haylage have to chop it at 60 percent moisture or higher in order to keep it from blowing away when they fill trucks. I take my crop to a local dehydrating plant that likes my lower moisture haylage because it reduces drying costs.
"When people see it for the first time many of them aren't sure what they're looking at. I cut about 4,000 tons of haylage every year so I save a lot of money on labor."
To modify the forage harvester, Alexander stripped it down to the cab, cutting mechanism, axles, and engine. He had to shorten the body of the harvester so the truck could be backed up against the spout. To do that he turned the engine sideways and also lowered it 2 1/2 ft. The engine originally drove a gearbox but now belt-drives the pickup and cutting mechanism. The engine also direct-drives a hydrostatic pump that drives a transmission - the final drive off a Gleaner combine - on the front axle. The rear wheels aren't powered. The steering is done by a separate hydraulic pump. It operates a pair of hydraulic cylinders that mount on each side of the steering axle and are connected to a tie rod. The steering axle consists of an 8 by 12-in. rectangular beam that pivots in the middle on a 3-in. dia. king pin. The front axle is also built from an I-beam.
The cab was originally mounted in the middle of the machine. Alexander moved it over to one side and also raised it 2 ft. He used steel I-beams to build a frame that supports the engine, cab, pickup, and cutting mechanism. He used more I-beams to build the 22-ft. long, 16-ft. wide deck and bolted and welded it to the frame on front. Deck is covered by 1-in. steel bar grating. The forage harvester was originally powered by a 240 hp engine. Alexander wanted more power so he replaced it with a 300 hp, 619 cu. in. diesel engine off a Deere 8640 4-WD tractor.
"It seems to have a million hoses on it," says Alexander. "Electric-hydraulics are used to control the steering, belt tension, raise and lower the ramp, pickup, power the cutting mechanism, and turn the forage harvester spout. Everything's operated by toggle switches in the cab."
Contact: FARM SHOW Followup, Gunther Alexander, Box 78, Vauxhall, Alberta, Canada T0K 2K0 (ph 403 654-2754).
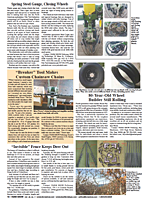
Click here to download page story appeared in.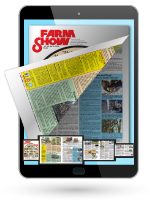
Click here to read entire issue
SP Forage Harvester Carries "Piggyback" Truck FORAGE HARVESTERS Forage Harvesters (31F) 23-1-1 When Gunther Alexander heads out to the field in his self-propelled forage harvester, he's not surprised when people stop on the road to stare. He knows no one's ever seen a rig quite like his.
The Vauxhall, Alberta, farmer-inventor carries a 3-ton truck on the back of his Deere 5400 harvester. When the truck gets full, he drives it off the 22-ft. deck and heads back to the farm.
The entire rig is 55 ft. long and 16 ft. wide and is equipped with big 30.5 by 32 flotation tires on front (off a Deere 8820 combine) and smaller tires on back. The rear axle is used for steering and there's a 12-ft. hydraulic-operated loading ramp on back.
Alexander blows the haylage into a 2-ft. opening at the back of the truck which has a 20-ft. long, 8-ft. high box. The forage harvester's spout actually extends inside the truck. The box raises hydraulically and dumps its load out through an 8-ft. wide door at the back.
"This setup lets me do the job alone or with one helper, and it eliminates the hassle of filling a truck on-the-go," says Alexander. "I generally use two trucks. An employee drives one truck to town while I fill the other one. Each truck can haul 10 tons of 40 percent moisture haylage.
"I use it on my own farm and I also do custom work for area farmers. Most farmers who chop haylage have to chop it at 60 percent moisture or higher in order to keep it from blowing away when they fill trucks. I take my crop to a local dehydrating plant that likes my lower moisture haylage because it reduces drying costs.
"When people see it for the first time many of them aren't sure what they're looking at. I cut about 4,000 tons of haylage every year so I save a lot of money on labor."
To modify the forage harvester, Alexander stripped it down to the cab, cutting mechanism, axles, and engine. He had to shorten the body of the harvester so the truck could be backed up against the spout. To do that he turned the engine sideways and also lowered it 2 1/2 ft. The engine originally drove a gearbox but now belt-drives the pickup and cutting mechanism. The engine also direct-drives a hydrostatic pump that drives a transmission - the final drive off a Gleaner combine - on the front axle. The rear wheels aren't powered. The steering is done by a separate hydraulic pump. It operates a pair of hydraulic cylinders that mount on each side of the steering axle and are connected to a tie rod. The steering axle consists of an 8 by 12-in. rectangular beam that pivots in the middle on a 3-in. dia. king pin. The front axle is also built from an I-beam.
The cab was originally mounted in the middle of the machine. Alexander moved it over to one side and also raised it 2 ft. He used steel I-beams to build a frame that supports the engine, cab, pickup, and cutting mechanism. He used more I-beams to build the 22-ft. long, 16-ft. wide deck and bolted and welded it to the frame on front. Deck is covered by 1-in. steel bar grating. The forage harvester was originally powered by a 240 hp engine. Alexander wanted more power so he replaced it with a 300 hp, 619 cu. in. diesel engine off a Deere 8640 4-WD tractor.
"It seems to have a million hoses on it," says Alexander. "Electric-hydraulics are used to control the steering, belt tension, raise and lower the ramp, pickup, power the cutting mechanism, and turn the forage harvester spout. Everything's operated by toggle switches in the cab."
Contact: FARM SHOW Followup, Gunther Alexander, Box 78, Vauxhall, Alberta, Canada T0K 2K0 (ph 403 654-2754).