You have reached your limit of 3 free stories. A story preview is shown instead.
To view more stories
(If your subscription is current,
click here to Login or Register.)
Elevated Hog Building Keeps Manure Dry
"It results in dry, reduced-odor manure that's a lot easier to handle than conventional liquid hog manure out of a pit. We've also found that our animals perform exceptionally well in this building," says Tom Menke, Greenville, Ohio, president of EnviroLogic Co., whose patented system for raising hogs like chickens is
..........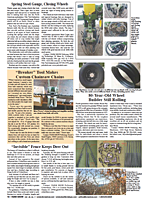
You must sign in, subscribe or renew to see the page.
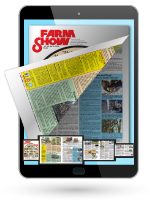
You must sign in, subscribe or renew to see the flip-book
Elevated Hog Building Keeps Manure Dry BUILDINGS Livestock 23-1-3 "It results in dry, reduced-odor manure that's a lot easier to handle than conventional liquid hog manure out of a pit. We've also found that our animals perform exceptionally well in this building," says Tom Menke, Greenville, Ohio, president of EnviroLogic Co., whose patented system for raising hogs like chickens is getting a lot of attention across the country.
Menke recently built a 45-ft. wide, 200-ft. long building with enough capacity for about 1,000 hogs. What makes the building unique is that it's two stories tall and doesn't have a below-ground manure pit. Instead, it has a ground-level manure processing area with a slatted floor 8 ft. above where the animals are kept.
The concrete manure floor has more than 3,200 aeration holes in it. Aeration fans and plenums are located at both ends of the building. Eight PVC tubes, 4 in. in dia. and spaced about 2 1/2 ft. apart, are embedded in the concrete manure floor and extend from each plenum the length of the building. Each tube has a series of holes on top. Air is forced up through holes in the concrete floor and then up through an 18-in. deep layer of absorbent material, such as wood shavings, which is under the manure. The material absorbs the urine and holds the feces during the drying process.
To remove manure, Menke opens doors on the side of the building and uses a skidsteer loader to scoop out the manure.
"It works much like the drying floor of a grain bin. Drying the manure creates a much better product that's more nutrient dense, easier to handle, and has less odor," says Menke. "The problem with hog manure has always been the excess water that's in it. With poultry manure, you only have to run air over the top of the manure to dry it. However, hog manure contains a lot of liquid so the air has to be forced up through the manure while the free liquids are being held in the absorbent material.
"One big advantage is that by drying the liquid in the manure, the smell is greatly reduced. Another advantage is that the dry manure is more concentrated and therefore requires a lower application rate per acre than conventional liquid manure. Pound for pound, dry hog manure is as nutrient-dense as poultry manure which makes it a valuable crop nutrient. Also, it can be handled like dry poultry manure and sold as a commodity.
"We've found that hogs really do well on this system. We put our first group of 45-lb. feeder pigs into the building last July. They were finished in an average of 113 days at a weight of 260 lbs., with a 1.84 lb. daily gain and a 2.5 lb. feed conversion ratio."
Menke says the elevated hog building de-sign costs about 12 percent more than a comparable conventional pit building. "It appears that the hog performance advantages, as well as the lower operational costs of handling the manure as a dry product rather than a liquid, more than compensate for the additional building costs."
He's working with a local building company which hopes to begin selling the new type of building soon.
Contact: FARM SHOW Followup, Tom Menke, Menke Consulting, Inc., 6070 Routzong Rd., Greenville, Ohio 45331 (ph 937 447-4225; fax 2225).
To read the rest of this story, download this issue below or click
here to register with your account number.