Hydraulically Operated Swather Header Cart
"When I bought a 1997 New Holland 2550 self-propelled swather, I quickly found out I didn't like driving down narrow roads with the 18-ft. header on the machine," says Albert Schoenberger who solved the problem by building a hydraulically operated header cart.
The Hereford, Texas, custom swather's main challenge was to come up with a cart that raised up to header level. That's because the swather has four flotation springs that prevent the header from being lowered onto a trailer.
He started out with a 20-ft. long cotton trailer, removing the bed and stripping it down to the 15-ft. chassis. He liked the trailer because it had low ground clearance.
He lengthened the trailer to 22 ft. with 2 in. dia. pipe to accommodate the 18-ft. header, which has an outside length of about 21 ft.
Next, he built a box subframe out of 4-in. sq., 3/16-in. wall tubing that mounts directly on top of the axles. He used four lengths of 6-in. channel iron to make vertical braces for each corner of the trailer to stabilize the header for loading and unloading.
Likewise, he used lengths of 4-in. channel iron attached to the top side of the axles and to the box subframe as horizontal stabilizers for transport. The channel iron attaches to the axles and subframe with 1 in. dia. steel pins and bushings so they raise and lower along with the subframe.
A pair of 2 1/2 by 24-in. hydraulic cylinders mount in sliding sleeves on each end. The cylinders are powered by an Army surplus hand pump, and their 24-in. stroke allows the header to be easily loaded onto the raised trailer.
"I raise the subframe and set the header on it," Schoenberger says. "By unhooking the header drive motor and header tilt cylinder, the swather is ready to back up from the header. When the swather is clear, I use a relief valve on the pump to lower the header to transport position. When I get to the next field, I use the hand pump to raise the header up and drive the swather under it. I lower the header partially and reattach the header lift cylinder and drive motor and then finish lowering the header onto the swather.
"The trailer makes it much easier to move from field to field and cuts down by as much as half on travel time between jobs because I'm able to travel faster."
Out-of-pocket expense was $750.
Contact: FARM SHOW Followup, Albert Schoenberger, Rt. 5, Box 111, Hereford, Texas 79045 (ph 806 289-5341).
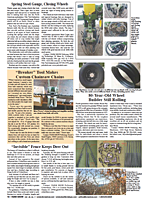
Click here to download page story appeared in.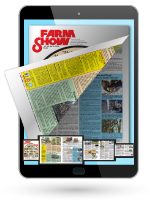
Click here to read entire issue
Hydraulically Operated Swather Header Cart SWATHERS Swathers 23-3-8 "When I bought a 1997 New Holland 2550 self-propelled swather, I quickly found out I didn't like driving down narrow roads with the 18-ft. header on the machine," says Albert Schoenberger who solved the problem by building a hydraulically operated header cart.
The Hereford, Texas, custom swather's main challenge was to come up with a cart that raised up to header level. That's because the swather has four flotation springs that prevent the header from being lowered onto a trailer.
He started out with a 20-ft. long cotton trailer, removing the bed and stripping it down to the 15-ft. chassis. He liked the trailer because it had low ground clearance.
He lengthened the trailer to 22 ft. with 2 in. dia. pipe to accommodate the 18-ft. header, which has an outside length of about 21 ft.
Next, he built a box subframe out of 4-in. sq., 3/16-in. wall tubing that mounts directly on top of the axles. He used four lengths of 6-in. channel iron to make vertical braces for each corner of the trailer to stabilize the header for loading and unloading.
Likewise, he used lengths of 4-in. channel iron attached to the top side of the axles and to the box subframe as horizontal stabilizers for transport. The channel iron attaches to the axles and subframe with 1 in. dia. steel pins and bushings so they raise and lower along with the subframe.
A pair of 2 1/2 by 24-in. hydraulic cylinders mount in sliding sleeves on each end. The cylinders are powered by an Army surplus hand pump, and their 24-in. stroke allows the header to be easily loaded onto the raised trailer.
"I raise the subframe and set the header on it," Schoenberger says. "By unhooking the header drive motor and header tilt cylinder, the swather is ready to back up from the header. When the swather is clear, I use a relief valve on the pump to lower the header to transport position. When I get to the next field, I use the hand pump to raise the header up and drive the swather under it. I lower the header partially and reattach the header lift cylinder and drive motor and then finish lowering the header onto the swather.
"The trailer makes it much easier to move from field to field and cuts down by as much as half on travel time between jobs because I'm able to travel faster."
Out-of-pocket expense was $750.
Contact: FARM SHOW Followup, Albert Schoenberger, Rt. 5, Box 111, Hereford, Texas 79045 (ph 806 289-5341).
To read the rest of this story, download this issue below or click
here to register with your account number.