Recycled Pipe Used To Create "Moveable" Feedlot
In an effort to keep his cattle pens from deteriorating, an Alberta feedlot operator designed an unusual system that gives him maximum layout flexibility, strength, and cost-effectiveness while virtually eliminating the need for fence maintenance.
Lorne Semler runs a 4,000 head feedlot and uses his home-built portable fencing panels for the entire lot. He got the idea after seeing a pasture catch pen based on the same basic concept.
The frame of each 30 by 5 ft. panel is made from oilfield drillstem pipe. The cross-pieces are made from sucker rod. Five upright posts, made from "sinker bar rod", provide added strength. Two 5-ft. wide "feet" are centered cross-wise under the frame, welded to the base of each post. They provide enough stability to keep cattle from knocking the fence panels over.
Semler's feedlot corrals consist of 500 portable panels, totaling 15,000 ft. or about three miles of iron fence. He says the system was less expensive to build than plank fence with the added advantage of being totally portable.
All components are welded together.
He purchased materials from oil companies and salvage outfits. Each panel cost him about $150 including material and labor. Panels weigh about 650 lbs. and are easily moved with a tractor and front end loader.
Semler tried to buy as much sucker rod with scrapers on it as possible, since it was slightly cheaper and the scrapers provide something for the cattle to rub on that can't be damaged.
"When the ground begins to deteriorate in the pens, I simply "pull" the pens and bring in a dozer to create a brand new surface," he says. "I can also resize a pen anytime I want."
The panels also work well as a "quick catch" system for cattle out on pasture where there are no handling facilities.
Semler expanded on his fence panel idea and modified it to create portable windbreak panels as well. He used a pipe frame of the same dimensions and bolted on three evenly spaced planks before nailing upright slabs onto the planks. Feet were positioned similarly on the bottom, but their length was extended to 8 ft. because the extra wind pressure demanded added stability.
A 10-ft. lifting bar is located at the top above the slabs to allow easy access for the teeth of a front end loader bucket. In this way, the panels can be lifted and moved around without the operator having to leave the seat of the tractor.
Semler says the windbreak panels work well and cost about $250 per panel for materials and labor.
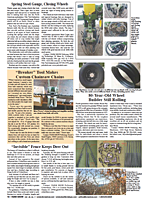
Click here to download page story appeared in.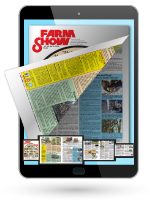
Click here to read entire issue
Recycled Pipe Used To Create "Moveable" Feedlot LIVESTOCK Beef 23-6-40 In an effort to keep his cattle pens from deteriorating, an Alberta feedlot operator designed an unusual system that gives him maximum layout flexibility, strength, and cost-effectiveness while virtually eliminating the need for fence maintenance.
Lorne Semler runs a 4,000 head feedlot and uses his home-built portable fencing panels for the entire lot. He got the idea after seeing a pasture catch pen based on the same basic concept.
The frame of each 30 by 5 ft. panel is made from oilfield drillstem pipe. The cross-pieces are made from sucker rod. Five upright posts, made from "sinker bar rod", provide added strength. Two 5-ft. wide "feet" are centered cross-wise under the frame, welded to the base of each post. They provide enough stability to keep cattle from knocking the fence panels over.
Semler's feedlot corrals consist of 500 portable panels, totaling 15,000 ft. or about three miles of iron fence. He says the system was less expensive to build than plank fence with the added advantage of being totally portable.
All components are welded together.
He purchased materials from oil companies and salvage outfits. Each panel cost him about $150 including material and labor. Panels weigh about 650 lbs. and are easily moved with a tractor and front end loader.
Semler tried to buy as much sucker rod with scrapers on it as possible, since it was slightly cheaper and the scrapers provide something for the cattle to rub on that can't be damaged.
"When the ground begins to deteriorate in the pens, I simply "pull" the pens and bring in a dozer to create a brand new surface," he says. "I can also resize a pen anytime I want."
The panels also work well as a "quick catch" system for cattle out on pasture where there are no handling facilities.
Semler expanded on his fence panel idea and modified it to create portable windbreak panels as well. He used a pipe frame of the same dimensions and bolted on three evenly spaced planks before nailing upright slabs onto the planks. Feet were positioned similarly on the bottom, but their length was extended to 8 ft. because the extra wind pressure demanded added stability.
A 10-ft. lifting bar is located at the top above the slabs to allow easy access for the teeth of a front end loader bucket. In this way, the panels can be lifted and moved around without the operator having to leave the seat of the tractor.
Semler says the windbreak panels work well and cost about $250 per panel for materials and labor.
To read the rest of this story, download this issue below or click
here to register with your account number.