Slide-In "Service Bed" Can Also Be Used In Shop
"When we're in the field, we pick it up with a forklift and slip it into the back of our pickup. At other times of the year I mount it on a dolly and use it in my shop," says Dwight Colson, Caledonia, Miss., about his "slide-in service bed".
It consists of a 4 by 8-ft. metal platform fitted with maintenance equipment. It fits snugly between the wheel wells of Colson's pickup. The front end of the platform slides under a permanently-mounted toolbox at the front of the bed.
The slide-in bed is fitted with a portable air compressor, air-operated grease gun, 50-gal. fuel tank, and three 120-lb. grease drums which are lined up against one side of the bed. A big garbage can stands alongside the drums. All of the equipment is secured to brackets welded onto the floor.
"Once the slide-in service bed is inside the bed and the tailgate is shut, it can't move and nothing on top of it can move, either," says Colson. "I spent about $300 on it, not including my labor. I use the compressor to clean out the air conditioner system on the cotton picker and to operate the grease gun. I had been using ropes to tie the same equipment down inside the pickup bed. The problem was that the equipment still bounced around a lot. One time the air compressor fell over and broke. It cost $100 to fix.
"I keep the three 120-lb. drums of grease on hand because my cotton picker requires both spindle grease and multi-purpose grease. It takes about 20 minutes to service a picker with spindle grease using the air-operated grease gun. A drum of spindle grease will last only about five days so I always carry a replacement drum."
Colson used 1/4-in. thick steel plate to make the unit's floor and two 8-ft. long pieces of square tubing to make the skids underneath it. He welded a 4-in. sq. section of channel iron between the two lengths of tubing at both ends and in the middle for reinforcement.
The grease drums mount between a side railing made from 2-in. channel iron and a length of box tubing welded to the floor. The drums are secured with a pair of nylon ratchet straps. A bracket on the railing is used to store the grease gun.
To mount the air compressor he welded a 7-in. high channel iron bracket onto the service bed floor, then removed the compressor wheels and inserted the axle through holes drilled into both brackets. The axle is secured by a cotter pin at each end. A nozzle holder next to one of the brackets is used to store the fuel pump nozzle. The fuel tank has flanges on the bottom and is bolted directly to the floor.
"I plan to add reels for my regular grease gun and for the air compressor hose," notes Colson.
Contact: FARM SHOW Followup, Dwight Colson, 860 Spruill Rd., Caledonia, Miss. 39740 (ph and fax 662 356-6631).
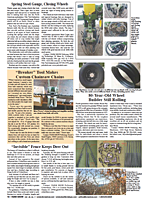
Click here to download page story appeared in.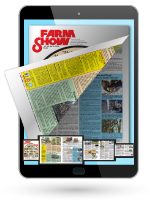
Click here to read entire issue
Slide-In "Service Bed" Can Also Be Used In Shop PICKUPS Accessories 24-2-41 "When we're in the field, we pick it up with a forklift and slip it into the back of our pickup. At other times of the year I mount it on a dolly and use it in my shop," says Dwight Colson, Caledonia, Miss., about his "slide-in service bed".
It consists of a 4 by 8-ft. metal platform fitted with maintenance equipment. It fits snugly between the wheel wells of Colson's pickup. The front end of the platform slides under a permanently-mounted toolbox at the front of the bed.
The slide-in bed is fitted with a portable air compressor, air-operated grease gun, 50-gal. fuel tank, and three 120-lb. grease drums which are lined up against one side of the bed. A big garbage can stands alongside the drums. All of the equipment is secured to brackets welded onto the floor.
"Once the slide-in service bed is inside the bed and the tailgate is shut, it can't move and nothing on top of it can move, either," says Colson. "I spent about $300 on it, not including my labor. I use the compressor to clean out the air conditioner system on the cotton picker and to operate the grease gun. I had been using ropes to tie the same equipment down inside the pickup bed. The problem was that the equipment still bounced around a lot. One time the air compressor fell over and broke. It cost $100 to fix.
"I keep the three 120-lb. drums of grease on hand because my cotton picker requires both spindle grease and multi-purpose grease. It takes about 20 minutes to service a picker with spindle grease using the air-operated grease gun. A drum of spindle grease will last only about five days so I always carry a replacement drum."
Colson used 1/4-in. thick steel plate to make the unit's floor and two 8-ft. long pieces of square tubing to make the skids underneath it. He welded a 4-in. sq. section of channel iron between the two lengths of tubing at both ends and in the middle for reinforcement.
The grease drums mount between a side railing made from 2-in. channel iron and a length of box tubing welded to the floor. The drums are secured with a pair of nylon ratchet straps. A bracket on the railing is used to store the grease gun.
To mount the air compressor he welded a 7-in. high channel iron bracket onto the service bed floor, then removed the compressor wheels and inserted the axle through holes drilled into both brackets. The axle is secured by a cotter pin at each end. A nozzle holder next to one of the brackets is used to store the fuel pump nozzle. The fuel tank has flanges on the bottom and is bolted directly to the floor.
"I plan to add reels for my regular grease gun and for the air compressor hose," notes Colson.
Contact: FARM SHOW Followup, Dwight Colson, 860 Spruill Rd., Caledonia, Miss. 39740 (ph and fax 662 356-6631).
To read the rest of this story, download this issue below or click
here to register with your account number.