2000 - Volume #24, Issue #4, Page #03
[ Sample Stories From This Issue | List of All Stories In This Issue | Print this story
| Read this issue]
Low-Cost Replacement Rolls Designed To Outlast Original Equipment
![]() |
![]() |
Seven years ago, he started a business in his hometown of Tea, South Dakota, repairing cast iron rolls from roller mills. Since then he's done work for roller mill and forage harvester owners from all over the U.S. and Canada.
After several years of regrooving and sharpening rollers, he decided he could make a better product than was commonly being used. He started making his own line of steel rollers. "I based my rollers on products I'd seen and serviced, but designed them to last longer," he says.
"We've been making kernel and crop processor rolls for three years, and annual sales are now three times what they were the first year. We sell to both individuals and companies. A number of after-market parts companies buy large quantities for resale.
"Our rolls are hardened throughout, not just on the surface. Once they've been hardened, they're put back into an oven and tempered to prevent brittleness. This process makes them extremely hard and much stronger than most original equipment rolls," he says.
One of the unique features he designed into his rollers is a separate shaft. "With other rolls, you often have to throw them out if there's a problem with the shaft. For example, if it's worn because of a bearing failure or gets bent. Our rolls have a replaceable shaft that can be repaired or replaced separately," he says.
Scherer Corrugating & Machine, Inc., makes rolls for Automatic, Bearcat and Henke roller mills and for most brands of forage harvesters. "The only one we don't make rolls for is Claas, and we are working on that one," he says.
Scherer says he commonly stocks rolls from 6 in. through 14 in. in outside diameter, and up to 52 in. long. And if his standard sizes aren't quite right, he can custom build new rolls to fit.
"We have a full machine shop, so we can repair most rolls with shaft or balance problems," he says. "Producers can typically save 10 to 20 percent with our rolls as compared to those from the manufacturer. One popular roller mill uses 9 in. dia. rolls that are 34 in. long and normally sell for $4,000 per pair. We sell them for $3,400."
In addition to sharpening, manufacturing and selling rolls, Scherer Corrugating & Machine also sells kernel processor conversion mills for older Gehl, Deere and New Holland silage cutters. "This is a bolt-on unit for pull-type and some self-propelled harvesters," he says. "After a lot of phone calls and questions, I'm convinced this is one of the best units available. And it sells for about 15 percent less than comparable kits on the market."
For more information, contact: FARM SHOW Followup, Bob Scherer, Scherer Corrugating & Machine, Inc., 27114 Grummand Ave., Tea, S. Dak. 57064 (ph 800 883-9790 or 605 368-2659; E-mail: corrugating@dtgnet.com; Web site: www.scherercorrugating.com).
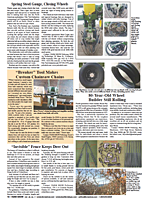
Click here to download page story appeared in.
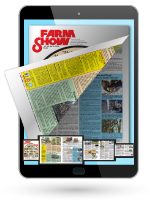
Click here to read entire issue
To read the rest of this story, download this issue below or click here to register with your account number.