You have reached your limit of 3 free stories. A story preview is shown instead.
To view more stories
(If your subscription is current,
click here to Login or Register.)
Gooseneck Hitch Pulls Disk Ahead Of Grain Drill To Eliminate Tracks
"My son Barry and I were having problems with compaction caused by the dual wheels on our 4-WD tractor whenever we planted barley. We solved the problem by building a gooseneck hitch that lets us pull an 18-ft. Deere offset disk ahead of the drill," says Bill Juhnke, Parkston, S. Dak.
The gooseneck hitch is 27 f
..........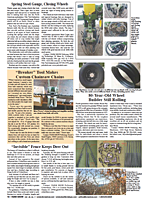
You must sign in, subscribe or renew to see the page.
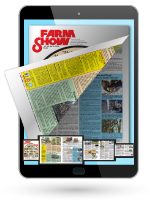
You must sign in, subscribe or renew to see the flip-book
Gooseneck Hitch Pulls Disk Ahead Of Grain Drill To Eliminate Tracks HITCHES Hitches 24-5-37 "My son Barry and I were having problems with compaction caused by the dual wheels on our 4-WD tractor whenever we planted barley. We solved the problem by building a gooseneck hitch that lets us pull an 18-ft. Deere offset disk ahead of the drill," says Bill Juhnke, Parkston, S. Dak.
The gooseneck hitch is 27 ft. long and was built out of 4 by 6-in., 1/4-in. thick rectangular tubing. It has a house trailer socket on front that attaches to a ball that's mounted on the tractor 3-pt. A pair of hydraulic hoses go through the hitch back to cylinders that are used to raise or lower the drill's lift assist wheels.
They also built their own 18-ft. grain drill by mounting three Deere 6-ft. pony press drills on a steel frame. They bought the drills equipped with square packer wheel shafts and mounted them inside a steel frame that they built out of 4 by 6-in. and 4 by 4-in. rectangular tubing. They used a 4-in. sq., 11-ft. length of tubing to build an axle that supports the lift assist wheels.
"We also use the drill to plant soybeans in 18-in. rows," says Juhnke. "We bought some plastic feed shut-offs from our Deere dealer and slipped them over the seed metering devices. We leave a pair of 24-in. wide ęskip rows' spaced six feet apart in case we have to drive through the field again after planting in order to spray or cultivate.
"The lift assist wheels are down only when the drill is on the road. In the field they're always up so that the drill's weight is always on the press wheels.
"We paid about $300 for each drill and spent about $600 to build the frame that supports them and the gooseneck hitch. We already had the hydraulic cylinders that are used to raise or lower the drill. We also bought about 100 ft. of hydraulic hose for about $160."
Contact: FARM SHOW Followup, Bill Juhnke, 42118 273rd St., Parkston, S. Dak. 57366 (ph 605 928-3209).
To read the rest of this story, download this issue below or click
here to register with your account number.