You have reached your limit of 3 free stories. A story preview is shown instead.
To view more stories
(If your subscription is current,
click here to Login or Register.)
Home-Built Hay Rake Saves Him a Bundle
"Even if you cut most of your hay with a mower-conditioner, you still need a rake around once in a while," says Bruce Parkes, Eriksdale, Manitoba.
He wanted one big enough to get the job done fast. He had a couple of older 5-wheel Vicon wheel rakes, but they were worn and small. When he priced new rakes,
..........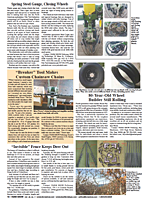
You must sign in, subscribe or renew to see the page.
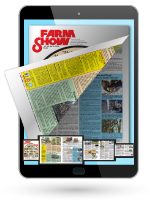
You must sign in, subscribe or renew to see the flip-book
Home-Built Hay Rake Saves Him a Bundle HAY & FORAGE HARVESTING Rakes 44 Even if you cut most of your hay with a mower-conditioner you still need a rake around once in a while says Bruce Parkes Eriksdale Manitoba He wanted one big enough to get the job done fast He had a couple of older 5-wheel Vicon wheel rakes but they were worn and small When he priced new rakes he decided he couldn t justify the expense Rather than buying a rake Parkes armed himself with his welder and a few pieces of new steel and combined the two old rakes into a single 10-wheel machine We made just about everything except the raking wheels he says He patterned it after Vicon s newer 9-wheel rake First he built a new frame from 4-in square steel tubing Then he added an arch of 3-in square tubing Finally he made axles for the raking wheels and ground wheels from new 1 1/4-in solid shafting I machined out the hubs on the 10 rake wheels so I could fit them with ball bearings Originally they had needle bearings and we were constantly replacing them The ball bearings were sealed but we popped the inside seals out of them so we could grease them through the zerks in the wheels he says Parkes put new-style Vicon springs on the rake wheels so they would float better He also stripped off all the old rake teeth and replaced them with current style teeth No modification was necessary to fit the new teeth to the old wheels The new rake has one rear transport wheel that he borrowed from a scrapped Versatile 103 swather He salvaged two wheels that were the same size from an old harrow bar to serve as front transport wheels For lift he put a 3-in piece of angle iron on the side of the main frame and ran a 1-in solid round shaft through that There are chains from the shaft to the axle to lift it He raises and lowers the raking bar using a hydraulic cylinder He used a double action cylinder for the lift but set it up as a single action cylinder by adding a oil reservoir made from a lawn mower gasoline tank to the retracting side of the cylinder Finally he used 2 1/2-in square tubing to make a tongue The rake picks up a swath about 18 ft wide It works very well he says We did have a little trouble with it wanting to walk sideways We decided it was because the front transport wheels were taking some of the weight off of the rear wheel We solved the problem by putting fluid in the tire and adding a couple of wheel weights over the top of it Parkes figures it cost him about $1 800 in new parts and steel to build the new rake in the spring of 1999 Parkes says while both rakes work well there are some things he might change On mine I d like to change the lift a little We have to be careful when we pick it up because sometimes the rake teeth hook in the lift chains he says We needed to make the knuckle at the back of the V-rake a little stronger It folds and pivots at that point We used 2-in diameter heavy-walled pipe and 1 1/4-in solid steel shaft to make it The pipe and shaft were heavy enough but we should have cut the pipe a little longer where we welded it to the rake frame That would have given it more strength and put less stress on it when it flexed Contact: FARM SHOW Followup Bruce Parkes Box 151 Eriksdale Manitoba R0C 0W0 Canada Ph 204 739-2616
To read the rest of this story, download this issue below or click
here to register with your account number.