2000 - Volume #24, Issue #6, Page #44
[ Sample Stories From This Issue | List of All Stories In This Issue | Print this story
| Read this issue]
Garden Tractor Flail Spreader
![]() |
![]() |
"I wasn't convinced a ground drive system would have enough power," says Martin, who spent less than $600 to build his flail-type spreader, not counting the engine. It holds between 25 and 30 bushels and it has enough power to tear apart packed manure from his steer pen.
Martin picked up a 250 gallon fuel tank from a nearby manufacturing company. Rejected for fuel storage, the tank was discounted to $100, and because it was new, he didn't have to worry about fumes when it came time to torch the opening.
The spreader's 8-ft. long frame was built out of 4-in. channel iron and designed to come to a point just ahead of the engine which is mounted at the front end of the unit. At the point, Martin mounted a 2-in. hitch receiver on the bottom side of the channel iron. He then designed a hitch with a 6-in. drop (similar to those found on camper trailers) which, when slid in upright, allows the spreader to be pulled behind his pickup truck, and when reversed, fits the drawbar of his garden tractor. When the unit is stored, it can be removed entirely to save space.
The frame mounts on a rear axle, spindles and wheels from a front-wheel drive car which Martin picked up at a local junkyard. The only change made before welding the axle to the frame was to shorten its length to 42 in. so the spreader would fit through Martin's 48-in. barn doors.
The tank itself was torched open with 66-in. horizontal cuts at the three o'clock and nine o'clock positions and 32-in. vertical cuts. The heavy 10 ga. steel in the tank meant that only the top edge, which was hinged to a flat 10 gauge lid, had to be reinforced. By hinging the lid and reinforcing it with 1-in. angle iron, it could be opened for easy filling and closed for spreading. Triangular wings welded to either end of the tank provided the base for the closed lid, and doing so, created the space for material to exit.
To create the flail bar, Martin welded 1-in. shafts to either end of a 2-in. steel pipe. High tensile, 1/4-in. chains were welded to opposite sides of the pipe at 5-in. intervals. A piece of 2 by 2-in. flat iron was then bolted to the end of each chain.
Martin mounted the pipe in place with four-bolt bearings at the center of either end of the barrel. A heavy V-belt running off the Kohler engine and through a jack shaft to reduce speed, drives the shaft at 300 rpm's. The two bearings on the main shaft and the two on the jack shaft, along with the V-belt, are the only likely wear points on the spreader. Minimal maintenance and simplicity were goals Martin had from the beginning.
"The whole project took about 20 to 25 hours, and I can pull the loaded spreader with my 10 hp Wheel Horse garden tractor."
Contact: FARM SHOW Followup, Ronald Martin, 260 Chestnut Hill Rd., Fredrericksburg, Penn. 17026 (ph 717 865-9604).
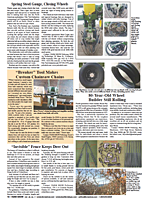
Click here to download page story appeared in.
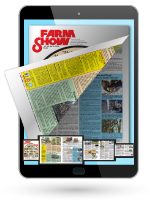
Click here to read entire issue
To read the rest of this story, download this issue below or click here to register with your account number.