You have reached your limit of 3 free stories. A story preview is shown instead.
To view more stories
(If your subscription is current,
click here to Login or Register.)
Hand-Made Knives Are Satin Finished
Edward M. Storch, RR 4, Mannville, Alberta, Canada T0B 2W0 (ph 780 763-2214): "My hand-made knives are satin finished and are in use world wide. I custom make them using the same "forge welding" process that was used by old time blacksmiths. The idea behind forge welding is to heat the metal, put the flux on, and hamme
..........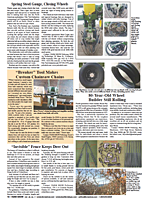
You must sign in, subscribe or renew to see the page.
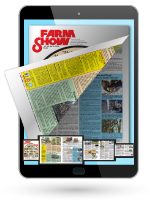
You must sign in, subscribe or renew to see the flip-book
Hand-Made Knives Are Satin Finished FARM HOME Miscellaneous 25-1-28 Edward M. Storch, RR 4, Mannville, Alberta, Canada T0B 2W0 (ph 780 763-2214): "My hand-made knives are satin finished and are in use world wide. I custom make them using the same "forge welding" process that was used by old time blacksmiths. The idea behind forge welding is to heat the metal, put the flux on, and hammer-weld objects together. Using this process I can take a piece of steel cable or roller chain from a farm machine, heat it, flux it, and forge weld it into a bar which I later turn into a knife. The pattern of the different types of alloys in the steels shows up in the finished product. It looks quite artistic. I could use more common coal forges, but they're hard to get and are messy to use. Using my propane-powered forge welding equipment I can have the material hot enough to weld in only about 10 minutes.
"I use a tangental venturi propane forge equipped with a central salt pot to heat treat the steel. It consists of a 16-in. long, 8 1/2-in. dia. steel pipe mounted on rollers. I line the inside of the pipe with a high temperature, heat-resistant fiber and cut a rectangular hole in the side of the pipe for the flame to exit. The flame cuts in at an angle and corkscrews around inside the pipe through a smaller 2-in. dia. pipe that's welded inside.
"After I've heated the steel I use a homemade 42-ton hydraulic press to shape it. The press is equipped with a 2-stage hydraulic pump and a 6-in. dia. hydraulic cylinder. It has a capacity of 16 gal. per minute at 600psi or 4 gal. per minute at 3,000 psi. I made different dies for the press which allow me to weld the material together flat or square. Or, I can use a homemade, air-operated, 65-lb. hammer that cycles up and down up to three times per second. Using both the hydraulic press and the air hammer makes for a much better end product.
"I also built my own 2 by 72-in. belt grinder for shaping the knives and for other general shop work. It's operated by a 2 hp electric motor.
"I teach knife-making classes in my shop. You can see examples of my work at my Website: www.Storchknives.com."
To read the rest of this story, download this issue below or click
here to register with your account number.