You have reached your limit of 3 free stories. A story preview is shown instead.
To view more stories
(If your subscription is current,
click here to Login or Register.)
Narrow Row Bean Planter
Warren Livingston, Fontanelle, Iowa, wanted to try narrow row soybeans, but couldn't justify the cost of a drill or narrow-row planter. He ended up building his own 8-row, 19-in. bean planter by an International 400 air planter with a Deere 7000.
"I call it my 7400 Max Air planter. It's small enough for our ope
..........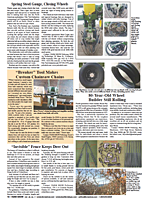
You must sign in, subscribe or renew to see the page.
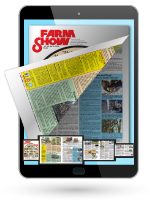
You must sign in, subscribe or renew to see the flip-book
Narrow Row Bean Planter PLANTERS Planters 25-1-42 Warren Livingston, Fontanelle, Iowa, wanted to try narrow row soybeans, but couldn't justify the cost of a drill or narrow-row planter. He ended up building his own 8-row, 19-in. bean planter by an International 400 air planter with a Deere 7000.
"I call it my 7400 Max Air planter. It's small enough for our operation and didn't cost much to build. It's about the same size as our 4-row, 38-in. corn planter so we can use the same grain head to harvest beans that we've always used."
Livingston bought an 8-row IH 400 planter at an auction for $200 and a used Deere 7000 4-row planter for $450. He bolted the IH row units and seed hoppers onto the Deere toolbar, leaving the Deere lift wheels, markers, and transmission in place. He cut out part of the frame and used gauge wheel brackets from a rotary hoe to make a frame that would work with the row unit lift rods.
He bought seed hopper mounts for an IH 500 planter at a salvage yard, cut them in half, and turned them around 180 degrees so the seed drum is at the front of the planter for easier monitoring. The IH planter was originally pto-driven. Livingston converted it to hydraulic drive using a 1,000 rpm hydraulic pump, motor, and cooler. To get the drum to turn in the right direction, he had to cut off the bevel gear on the drum's input shaft and mount it back on the right side of the seed drum's driveshaft.
"I built it four years ago and have had excellent stands with it every year," says Livingston. "A lot of people turn their heads when they first see it. I've displayed it at the Iowa State Fair three times and won several awards for it.
"My total investment the year I built it was only about $1,300. I spent $650 for both planters, $350 for hydraulic hoses, and $300 for the pump, motor, cooler, mounting brackets, and miscellaneous parts. Over the years I've made improvements that have boosted my total cost to about $2,150. The row units are staggered in pairs and there's only one disc closer per row unit for better trash flow. It has excellent trash clearance. In fact, I haven't plugged this planter up yet. The seed hopper holds 11 bu. of soybeans, which is enough for about 10 acres at a time.
"The hardest part of the project was finding the right gears to drive the seed drum," says Livingston. "The 400 planter's drive wheel had a 15-tooth sprocket that drove a 12-tooth sprocket on the jackshaft. The transmission had a 12-tooth sprocket that drove a 15-tooth sprocket on the drum's seed module input shaft. However, on the Deere planter, a 12-tooth sprocket drives a 16-tooth sprocket from the drive wheel to the transmission. To drive the seed drum correctly, I mounted a 16-tooth sprocket on the transmission and a 12-tooth sprocket on the seed drum. The number of seeds per acre came out almost dead perfect."
Contact: FARM SHOW Followup, Warren Livingston, 1753 Fontanelle Rd., Fontanelle, Iowa 50846 (ph 515 745-2009).
To read the rest of this story, download this issue below or click
here to register with your account number.