You have reached your limit of 3 free stories. A story preview is shown instead.
To view more stories
(If your subscription is current,
click here to Login or Register.)
"Owner's Report" On Do-It-Yourself Sawmills
Long-time FARM SHOW readers are familiar with Bill Reeks of Cromwell, Ky., creator of the do-it-yourself bandsaw mill. He built his first sawmill for less than $100, running the bandsaw blade around a pair of auto tires. We first featured Bill's machine six years ago. Since then, he's sent out more than 4,000 packets
..........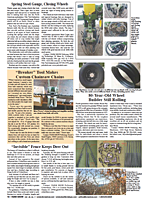
You must sign in, subscribe or renew to see the page.
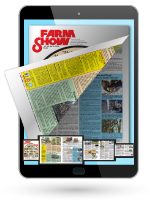
You must sign in, subscribe or renew to see the flip-book
"Owner's Report" On Do-It-Yourself Sawmills WOODLOT EQUIPMENT Miscellaneous 25-4-28 Long-time FARM SHOW readers are familiar with Bill Reeks of Cromwell, Ky., creator of the do-it-yourself bandsaw mill. He built his first sawmill for less than $100, running the bandsaw blade around a pair of auto tires. We first featured Bill's machine six years ago. Since then, he's sent out more than 4,000 packets of information to interested sawmillers and figures that more than half those went on to build their own sawmills.
We tracked down some of these bandsaw builders to see if they're satisfied with their "made it myself" mills and to find out what they're doing with them.
Bill is "notorious" for his ultra-personal customer service. His "packets" of information contain hundreds of photos and detailed information. And Bill is always available to help anyone who "gets stuck" along the way.
For an introductory packet about both of his bandsaw mills, you can send $3.00 in the U.S. or $4.00 in Canada (U.S. funds only). Complete information packets sell for $48.50 in U.S. funds only (add $2.50 in Canada). Contact: FARM SHOW Followup, Bill Reeks, Yellow-Jak-It, 7104 U.S. Hwy 231, Cromwell, Ky. 42333 (ph 270 274-3361).
Here's how our story shaped up:
Jerry Baker, Boar, Ala.: "I've cut a lot of logs with it and it has done a great job," says Baker, who's building a new home with his bandsaw mill. He used 13-in. wheels and a 13 hp vertical shaft engine salvaged from a Cub Cadet garden tractor.
"I use it to saw pine trees averaging 8 to 10 in. in diameter. Some of them are up to 14 ft. long. It cuts the boards so smooth I don't even have to plane them.
"I basically followed Reeks' plans, but as I was building the machine I would look it over and try to come up with something better. The main improvement I made is how I raise the platform up or down so the blade always stays true, which results in an entire board with even thickness. Whenever I turn the handle, the blade stays good and tight wherever I put it. As a result, I can cut as thin as 1/8-in. thick. Reeks has his blade-carrying platform attached to a cable and you can't move it just a little, you have to move it a lot. I run threaded bolts into nuts that I welded onto the frame and put a handle on top. A chain goes from one side to the other so both sides turn together.
"I've found that it's very important to keep the correct air pressure in the tires in order to maintain an even board thickness. If I did it over I'd use a horizontal shaft engine so I could use a straight belt. With my vertical shaft engine I have to twist the belt so it doesn't run as smooth and also wears more.
"I spent only about $400 to build my mill."
Contact: FARM SHOW Followup, Jerry Baker, 84 Bluff Dr., Boaz, Ala. 35957 (ph 256 593-5655).
E.T. Ash, College Station, Texas: He's happy with his bandsaw mill.
"I built it at a friend's junk yard and used a few parts from his ĉinventory'. I used the frame of a hydraulic press and 20-ft. lengths of angle iron. I had to go through a half dozen tires to find one that was straight enough to run true. I ended up using 14-in. Mazda car tires.
"A 7 1/2 hp electric motor drives the blade. I built and wired the starter with a friend's help and added a 24-volt DC circuit to energize the starter and to power a 24-volt motor that drives the head up and down. I push the head down the track manually, although eventually I plan to use the same type of DC motor to propel the carriage. I modeled the blade guides on a Wood Mizer unit. I plan to use the wood I cut to build some small timber-framed houses."
Contact: FARM SHOW Followup, E.T. Ash, 6690 River Oaks Drive, College Station, Texas 77845 (ph 979 690-1761).
John Anderson, Wilmot, S. Dak.: He uses his bandsaw mill to cut logs from 32 to 36 in. in diameter and up to 22 ft. long.
"It works great. I used most of Reeks's plans but made some modifications. I used 4 by 3-in. angle irons to make the main frame. My mill sets on the rear axle from a junked-out front wheel drive car. The steering wheel
To read the rest of this story, download this issue below or click
here to register with your account number.