You have reached your limit of 3 free stories. A story preview is shown instead.
To view more stories
(If your subscription is current,
click here to Login or Register.)
Tree Planter Made From Scrap Parts
With 16 acres of Christmas trees, Gary Albertson has plenty of use for a reliable tree planter. But when he needed a new one, he was reluctant to put out the kind of cash it would take to buy one.
Instead, Albertson, who also operates a welding shop in Fergus Falls, Minnesota, figured he could build his own fo
..........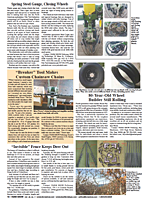
You must sign in, subscribe or renew to see the page.
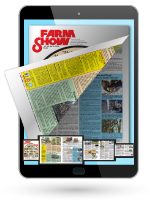
You must sign in, subscribe or renew to see the flip-book
Tree Planter Made From Scrap Parts PLANTERS Planters 26-1-4
With 16 acres of Christmas trees, Gary Albertson has plenty of use for a reliable tree planter. But when he needed a new one, he was reluctant to put out the kind of cash it would take to buy one.
Instead, Albertson, who also operates a welding shop in Fergus Falls, Minnesota, figured he could build his own for a lot less money.
He started with the main beam from an old pull-type plow. He stripped off everything but the shank. Then he built a frame and 3-pt. hitch for the beam and mounted a 20-in. coulter he bought at a local farm supply store in front of the shank.
He made wings to open a furrow from a 20 by 16-in. sheet of 1/4-in. steel by cutting it in half from opposite corners, to make two triangles. "I heated them and bent them into a curved wing shape and then welded them to the plow shank, just about an inch up from the tip," he says.
Behind the shank, he attached two 480 by 8-in. pneumatic trailer tires on wheels. "I found them in a junkyard. The axle was bent, but I needed only the stub shafts. I welded the stub shafts to the side of the tree planter, one on each side, tilted at about 30 degrees in at the bottom, to make press wheels to push the soil back in and firm it up around the seedlings," he says. Because the press wheels are welded to the planter, they act as gauge wheels and never let the shank go too deep.
Using scrap steel he had on hand, he built two adjustable seat mountings to support a couple of plastic bucket boat seats he bought at Wal-Mart. He made foot rests for the two riders from heavy gauge welded wire panels. On the frame in front of the seats, he mounted brackets to hold four 5-gal. plastic buckets. He made the brackets using old clutch bands he found in the junkyard that were just the right diameter to hold the buckets.
"Older tree planters had steel boxes for the seedlings. When we get trees in, we put them in a solution in 5-gal. buckets until we plant them. That always meant we had to take the trees out of the buckets and put them in the box on the planter. It takes time, it's messy, and the roots didn't always stay moist. This way, we just put four buckets on the planter and go. And there's nothing to clean up when we're finished," he says.
By itself, Albertson's tree planter weighs only about 300 lbs. He pulls it with a 25-hp four-wheel-drive diesel tractor, but says a similarly powered two-wheel drive could probably handle it. "With our hilly terrain, we've found the four-wheel drive tractor helps us get up and down hills and make straighter rows," he notes.
He says a crew of three (a driver and two people on the planter) can easily set 4,000 seedlings a day. And he believes it could be used for transplanting a number of other perennials and annuals like onions and vegetables.
He figures the planter cost him less than $200 in new materials and parts, but most of what he used was from the scrap pile and the junkyard. He guesses it took 30 hours or so to put it all together.
Contact: FARM SHOW Followup, Gary Albertson, Isanti Engineering, 715 W. Birch Ave., Fergus Falls, Minn. 56537 (ph 218 739-4949).
To read the rest of this story, download this issue below or click
here to register with your account number.