2003 - Volume #27, Issue #5, Page #34
[ Sample Stories From This Issue | List of All Stories In This Issue | Print this story
| Read this issue]
Self-Propelled Bale Handler"Makes It Easy"
![]() |
![]() |
It took most of his spare time over a couple of winters, but he ended up with a self-propelled bale handler that he figures will give him years of service.
The Cortez, Colorado, man started his project with a 2 1/2-ton single axle Chevrolet straight truck. "I stripped it down to the frame and shortened it," he says.
He wanted to make his loader steer from the rear with the drive axle in the front, so he turned the rear end over to make the differential operate backward from the original.
He replaced the original truck engine and transmission with a Chevy 305 cu. in. engine and an automatic transmission and transfer case salvaged from a 3/4-ton 4-WD pickup. "The loader is only 2-WD, but I wanted to be able to use the transfer case from the pickup so I'd have a low and high range," he says.
Over the drive axle, he mounted a GB Hi-Lift loader that he bought used. Then he built heavy-duty forks for the loader.
He says the old truck tires were in reasonable shape, so he left them all in place. He left the duals on the drive axle.
Weyand added a floorboard, seat and steering wheel on a pedestal to make an open operator's station just behind the forks, in front of the rear-mounted engine. He designed a hydraulic steering system for the loader.
Under the seat, he added a heater salvaged from a Peterbilt truck. It puts out enough heat to keep him warm on cold winter days, although the operator's station is open.
He also bought a new hydraulic pump sized to handle both the steering and the fork. He built an adapter to mount on the front of the engine so the hydraulic pump is driven from the crankshaft. "I put a splitter in the line to divide the flow between steering and the fork," he notes.
He added a 3-spool control valve that allows him to raise and lower the forks, set the teeth, and tilt the head to assist in picking up or setting bales down
He knew he'd need his hands for operating the hydraulic controls and steering, so he devised a foot-controlled shifter. He put a lock-out on the shifter so he can't accidentally shift into park. "I still have to shift ranges with a hand lever, but I can go from forward to reverse using the foot pedal," he explains.
He used a beer keg for a gasoline tank and made a 10-gal. hydraulic reservoir out of 1/8-in. plate steel. It fits into a space on the right side of his seat. He put the battery box to the left of the seat so it would be handy.
He added individual brake pedals for the front drive wheels, like those on a tractor. "I figured it would be handier for turning, but most of the time, the brake pedals are locked together," he says.
The loader picks up 18 two-wire bales at a time, allowing him to load a semi in a matter of just a few minutes. The only problem was the old 305 cu. in. engine had too little power. "I knew it was worn out when I put it in, but it was convenient at the time," he says. "And it just didn't have the torque at lower speeds that the loader required."
He's replacing the engine with a 350 Chevy, which he figures will have both the power and torque needed.
Weyand says the biggest problem in converting the old truck frame into a loader was the lack of available parts. "I ended up making most of the parts I needed to piece this together," he says.
He figures he has between $7,000 and $8,000 invested in the loader, including the price of the replacement 350 engine. "The biggest single expense was that loader frame," he says.
Contact: FARM SHOW Followup, Troy Weyand, 175 Hwy 160 S., Cortez, Colo. 81321 (ph 970 565-8714).
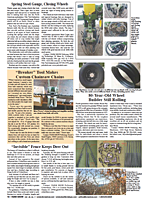
Click here to download page story appeared in.
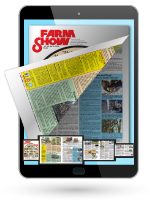
Click here to read entire issue
To read the rest of this story, download this issue below or click here to register with your account number.