2003 - Volume #27, Issue #5, Page #35
[ Sample Stories From This Issue | List of All Stories In This Issue | Print this story
| Read this issue]
He Put Together His Own Grain Handling System
![]() |
A 6-in. auger at the bottom of the dump pit lifts wet grain up to a nearby 2,700-bu. holding bin that he made out of an old storage bin and a home-built hopper bottom.
The fuel tank dump pit is buried in the ground at a 45-degree angle. It sets 22 ft. deep in the ground and is weighted down with 3-ton cement anchors because otherwise the freezing and thawing of the ground would cause it to work it's way up out of the ground.
"I can dump an entire semi load of grain into the dump pit at a time and go right back to the field," says Cohrs.
He paid $200 for the fuel tank which he got from a local bulk petroleum plant. He used a pressure washer to clean out the tank, then cut a 4-ft. sq. hole out at the top and installed a metal grate in it. The tank is supported by angle iron uprights.
To anchor the tank, he used a big form to make 2-ft. thick, 6-ft. sq. chunks of cement which he buried deep in the ground 10 ft. off to either side of the tank. He then welded a 5/8-in. dia. shaft into the tank and anchored it in the cement slab to hold the tank down. He also installed drain tile 10 ft. deep all around the entire area and installed a sump pump as well.
To waterproof the auger, he mounted it inside a 1/4-in. thick metal pipe that's welded into the top of the tank. He also welded steel plating on top of the tank to collect moisture that would otherwise condense on top of the tank. "About 10 to 15 gal. of moisture collects on top of the plating. Every fall I use a wet vac to remove the water," notes Cohrs.
An automated system complete with built-in relay-delays keeps grain flowing into the above-ground holding bin as neede.
He made the 2,700-bu. grain holding bin by using the sides and roof off an old 15-ft. dia., 18-ft. high bin and mounting it on top of a cone that he made from new sheet metal. The 25-ft. tall unit mounts on homemade steel legs that are embedded in a cement slab.
The bin bolts to a circular-shaped angle iron that's welded onto a steel ring made out of 8-in. wide, 1/4-in. thick flat rolled steel. The ring is welded to seven steel legs made out of 5 by 5, 1/8-in. thick wall tubing.
Cohrs had a local machine shop use 1/8-in. steel plate to make the cone, which has a 45-degree angle. They sheared the plating into pie-shaped pieces which were then curved and welded together. The cone's bottom outlet was made out of a length of 16-in. dia. steel pipe. A homemade slide gate is used to control grain flow.
"I probably built the cone much heavier than I needed to, but I wanted to make sure it would withstand the pressure of all that corn without buckling," says Cohrs.
Contact: FARM SHOW Followup, Kevin Cohrs, 6468 90th St., Glencoe, Minn. 55336 (ph 320 864-5780; email: Cohrsfarms@ hotmail.com).
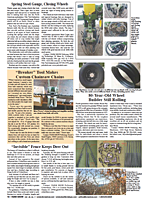
Click here to download page story appeared in.
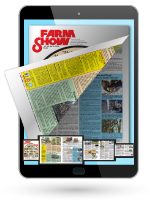
Click here to read entire issue
To read the rest of this story, download this issue below or click here to register with your account number.