You have reached your limit of 3 free stories. A story preview is shown instead.
To view more stories
(If your subscription is current,
click here to Login or Register.)
Home-Built Old-Time Cider Press
"While reminiscing some time back with my brother Brian we remembered how great it was to make homemade apple cider on a press, especially on cold winter days," says Jim Shephard. "By the end of that evening we had a plan to build our own press that we could share with our families for many more years to come," he says
..........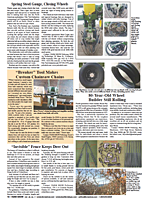
You must sign in, subscribe or renew to see the page.
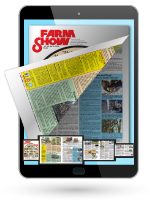
You must sign in, subscribe or renew to see the flip-book
Home-Built Old-Time Cider Press FARM HOME Food 28-2-40 "While reminiscing some time back with my brother Brian we remembered how great it was to make homemade apple cider on a press, especially on cold winter days," says Jim Shephard. "By the end of that evening we had a plan to build our own press that we could share with our families for many more years to come," he says.
"The basic frame is made of 4-in. square tubing and measures 48 in. tall and 38 in. wide. The gussets, table and press plates are made mostly from 3/8-in. stock sheet steel. We used stainless steel for the guide-rods that fit in machined tubes that were bored out to accept pressed-in bearing guides. A 12-ton hydraulic jack provides the power," says Shephard.
"The juice drains out on a plywood board drilled and routed out for drainage and coated with many layers of shellac. The juice falls into a strainer funnel and through to a bucket.
"The only pre-processing we do is grinding, which is taken care of with a 1 hp garbage disposal, that's used only for the press. We lowered the height of the cutting blade by half to reduce wear on the motor," Shephard notes.
"The pulp is layered into three 42-sq. in., 100 percent cotton sack cases. The cases are placed between squeeze boards and shoved under the press plate. One switch turns the press on and produces about 2 1/2 gal. of cider per bushel. We store the cider in plastic jugs," says Shephard.
Contact: FARM SHOW Followup, Jim Shephard, 6323 Marshall Road, Dexter, Mich. 48130 (ph 734-663-3399; email: jlshep@sbcglobal.net).
To read the rest of this story, download this issue below or click
here to register with your account number.