Monster Auger A Match For Any Truck
Tad Ziehm and Merrill Upchurch can move 800 bu. of grain in 10 min. with their self-propelled auger. And the 14-in. diameter auger not only moves grain fast, it moves it high, reaching up to 45 ft. above the ground. Best of all, when they need to move from one bin to another, it's a breeze. They can zip down the highway at speeds up to 22 mph.
"We were tired of pulling an auger behind a 4020 Deere in the freezing cold," explains Ziehm, who farms with Upchurch. "We had just bought a new combine and had the old 7700 combine sitting there. Merrill said he thought a self-propelled auger might be the way to go, so we sketched it out on the shop floor."
The result of Ziehm and Upchurch's brainstorming was their monster auger. Everything about it seems oversized. The frame is made from 3 by 6-in. boxed beams. The 76-ft. bin auger and 18-ft. fill auger were made from steel pipe 3/8-in. thick that weighs 70 lbs./ft. The pipe is normally used for highway billboards. Custom made flighting alone weighs 600 lbs.
A 22-ft. section at the end of the 76-ft. auger folds back on top of the main auger when in transit. An I-beam runs the length of the auger-pipe to add strength. Two steel cables suspended right above the hydraulic lift cylinder also provide support.
"It's strong enough that we could mount a fork lift or frame ęcherry picker' at the end of the main section," says Ziehm. "We plan to put a cat-walk along the top so we can climb up bins."
The big telescoping cylinder used to raise and lower the main auger was taken from a dump truck. The gearbox that runs the main auger is from a 9600 combine. The entire unit is powered by an engine and transmission from the 7700 Deere combine.
"We kept the transmission and the axles, but put the rear axle in front and the front axle at the rear," explains Ziehm.
The engine and cab were remounted on two I-beams that bolt to the machine's new frame. The engine faces forward, 3 to 4 feet ahead of the rear axle.
The transmission was reconnected to maintain the original gearshift pattern. The idler pulley is still in place, but mounted to the axle instead of the side of the combine. The drive belts had to be lengthened to account for the change in engine position.
The combine's former header cylinders are used to raise the 18-ft. fill auger on back. They made a new hydraulic fluid reservoir. The original reservoir is now a hydraulic filtering tank.
"The steering pump is used to power the steering and also to power the fill auger while the main auger is driven by the counter shaft from the 7700 engine."
One of the trickiest parts was the pivot point where the main auger connects to the machine. The men built a heavy pivot using a 6 5/8-in. dia. axle pipe secured between a framework made from I-beams and steel plate. Once the pipe was secured, they cut the center section out and mounted the 9600 combine cylinder drive gearbox at the center to drive the auger. By waiting until the axle was in place before cutting it, they knew the axle sections were in-line and true to each other.
Ziehm then used pieces of the same size pipe to make saddles or yokes for the axle. Each piece was sliced in half lengthwise, with the edges curled back to form flanges and drilled for bolts. One set was welded to the upright framework. The other was bolted down over the top of the auger housing axle. These allow the auger to pivot up and down.
The two wanted the feeder auger free to pivot into place also. This required attaching it to the auger housing with a series of plates that allow it to spin freely.
Wheels are mounted to the hopper at the lower end of the feeder auger. The mounts are at an angle that allows the wheels to roll in a perfect circle and allows the feeder auger to spin 180_ on the ground. For transport, Ziehm simply pushes the feeder auger back over the hydraulic cradle to be lifted free of the ground.
Three levers inside the cab operate the hydraulics to raise and lower the feeder auger, raise and lower the main auger and fold and unfold the extension.
"In the futur
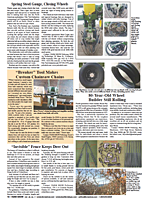
Click here to download page story appeared in.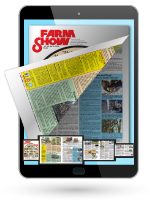
Click here to read entire issue
Monster Auger A Match For Any Truck AUGERS Augers (29B) 28-5-26 Tad Ziehm and Merrill Upchurch can move 800 bu. of grain in 10 min. with their self-propelled auger. And the 14-in. diameter auger not only moves grain fast, it moves it high, reaching up to 45 ft. above the ground. Best of all, when they need to move from one bin to another, it's a breeze. They can zip down the highway at speeds up to 22 mph.
"We were tired of pulling an auger behind a 4020 Deere in the freezing cold," explains Ziehm, who farms with Upchurch. "We had just bought a new combine and had the old 7700 combine sitting there. Merrill said he thought a self-propelled auger might be the way to go, so we sketched it out on the shop floor."
The result of Ziehm and Upchurch's brainstorming was their monster auger. Everything about it seems oversized. The frame is made from 3 by 6-in. boxed beams. The 76-ft. bin auger and 18-ft. fill auger were made from steel pipe 3/8-in. thick that weighs 70 lbs./ft. The pipe is normally used for highway billboards. Custom made flighting alone weighs 600 lbs.
A 22-ft. section at the end of the 76-ft. auger folds back on top of the main auger when in transit. An I-beam runs the length of the auger-pipe to add strength. Two steel cables suspended right above the hydraulic lift cylinder also provide support.
"It's strong enough that we could mount a fork lift or frame ęcherry picker' at the end of the main section," says Ziehm. "We plan to put a cat-walk along the top so we can climb up bins."
The big telescoping cylinder used to raise and lower the main auger was taken from a dump truck. The gearbox that runs the main auger is from a 9600 combine. The entire unit is powered by an engine and transmission from the 7700 Deere combine.
"We kept the transmission and the axles, but put the rear axle in front and the front axle at the rear," explains Ziehm.
The engine and cab were remounted on two I-beams that bolt to the machine's new frame. The engine faces forward, 3 to 4 feet ahead of the rear axle.
The transmission was reconnected to maintain the original gearshift pattern. The idler pulley is still in place, but mounted to the axle instead of the side of the combine. The drive belts had to be lengthened to account for the change in engine position.
The combine's former header cylinders are used to raise the 18-ft. fill auger on back. They made a new hydraulic fluid reservoir. The original reservoir is now a hydraulic filtering tank.
"The steering pump is used to power the steering and also to power the fill auger while the main auger is driven by the counter shaft from the 7700 engine."
One of the trickiest parts was the pivot point where the main auger connects to the machine. The men built a heavy pivot using a 6 5/8-in. dia. axle pipe secured between a framework made from I-beams and steel plate. Once the pipe was secured, they cut the center section out and mounted the 9600 combine cylinder drive gearbox at the center to drive the auger. By waiting until the axle was in place before cutting it, they knew the axle sections were in-line and true to each other.
Ziehm then used pieces of the same size pipe to make saddles or yokes for the axle. Each piece was sliced in half lengthwise, with the edges curled back to form flanges and drilled for bolts. One set was welded to the upright framework. The other was bolted down over the top of the auger housing axle. These allow the auger to pivot up and down.
The two wanted the feeder auger free to pivot into place also. This required attaching it to the auger housing with a series of plates that allow it to spin freely.
Wheels are mounted to the hopper at the lower end of the feeder auger. The mounts are at an angle that allows the wheels to roll in a perfect circle and allows the feeder auger to spin 180_ on the ground. For transport, Ziehm simply pushes the feeder auger back over the hydraulic cradle to be lifted free of the ground.
Three levers inside the cab operate the hydraulics to raise and lower the feeder auger, raise and lower
To read the rest of this story, download this issue below or click
here to register with your account number.