You have reached your limit of 3 free stories. A story preview is shown instead.
To view more stories
(If your subscription is current,
click here to Login or Register.)
Combo Tool Finishes Min-Till Fields
Getting fields in shape for planting gets tougher the more trash is left on the field. When Steve Weaver and his dad Gordon first made the switch to minimum till, they tried all the options, but no tool did the job quite right. So they decided to build their own.
The Weavers started with a Brady field cultivator
..........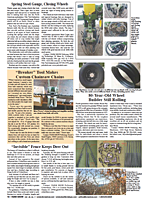
You must sign in, subscribe or renew to see the page.
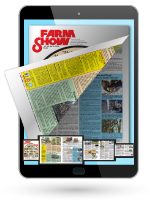
You must sign in, subscribe or renew to see the flip-book
Combo Tool Finishes Min-Till Fields TILLAGE EUIPMENT New Tools 29-1-28 Getting fields in shape for planting gets tougher the more trash is left on the field. When Steve Weaver and his dad Gordon first made the switch to minimum till, they tried all the options, but no tool did the job quite right. So they decided to build their own.
The Weavers started with a Brady field cultivator and added rolling harrows from Unverferth. "The unit worked pretty good, but we wanted to get the cornstalks worked up a little more," recalls Steve. "We bought a used disk and mounted a couple gangs on the front of the cultivator. That worked better, but we started breaking shafts on the disks."
The solution was to lengthen the frame on the field cultivator by about four feet and rig up a set of springs to allow the disc gangs to flex. The hitch on the field cultivator was bolted to the main frame. To lengthen it, they simply unbolted it and had three 4-ft. long pieces of similar sized tubing fabricated with faceplates to match and bolted them into place.
A 3 by 3-in. steel tubing cross piece on the hitch both reinforced the hitch and originally anchored the first rank of spring shanks. Once the frame was lengthened, the Weavers used the crosspiece as the front support for the disc gangs. They welded a second piece of tubing to the crosspiece to raise the disc gangs as they originally cut deeper than needed. Similar crosspieces were mounted on the extended frame to provide rear support for the gangs. This rear support consisted of two sections of 3 by 3-in. tubing mounted at a slight angle so the discs, when mounted, would throw dirt out from the center.
Four lengths of 6-in. channel iron were welded from front to rear gang supports. The gangs themselves are each mounted to two steel tubes, which are hinged at the rear cross support and suspended from a spring at the front. The springs came off an old IH 815 grain head. They rest on the topsides of the channel irons. A steel tube inside and two thirds the length of the spring acts as a guide for the spring. Threaded rods extend from the gang mount through the channel iron and the spring to a plate on top of the spring and a nut threaded to the rod.
"The springs let the gangs flex more," says Steve. "We simply tighten the nuts to take play out of the springs and gang movement."
A cross bar at the rear of the frame extension provides support for the frame. It also allows spring teeth to be offset on two different bars of the frame. Extending the frame and mounting the gangs farther forward better offset the weight of the rolling harrows.
"The entire unit is pretty well in balance," says Steve. "We also added a hitch to the rear so we can pull a packer behind as needed."
Weaver estimates their total investment at about $3,500. That included the cost of the original field cultivator, harrows and disc gangs.
Contact: FARM SHOW Followup, Steve Weaver, 4270 Kidron Road, Dalton, Ohio 44618 (ph 330 857 5641; email: samaweaver @aol.com).
To read the rest of this story, download this issue below or click
here to register with your account number.