"Roller Mill Bagger" Does Two Jobs
Running corn through a roller mill and then loading it into a bagger can be a great way to store feed, but doing it is a hassle. Because a bagger slowly moves ahead as the silage bag fills, the roller mill and the wagon emptying into it have to roll ahead as well.
"We had to have a tractor on the mill and one on the bagger," recalls David Weaver, who does custom bagging of shelled corn and silage as well as custom baling and manure application. "I figured that by putting a roller mill on top of the bagger, I would only need one tractor. It might not be any faster, but it would be a lot simpler."
Weaver began by ordering a custom-built roller mill from Isaac H Nolt, Leola, Penn. at a cost of about $8,500. It's designed to fit atop the bagger.
His plan was to adapt the 1,000-rpm roller mill to his 540-rpm bagger. It didn't work as well as he had hoped. So, he got Kelly Ryan Equipment Company to customize a bagger to run at 1,000 rpm's.
"The bagger came with a conveyor and a shield over the hopper," says Weaver. "I took the conveyor and shield off and adapted them so they could be reconnected again when needed for silage bagging."
He welded two flanges to a heavy crossbeam that runs across the rear of the bagger hopper. The 2 by 3-in. high pieces of 1/2-in. steel plate had holes drilled in them to match holes in the rear of the roller mill frame. Two 1/2-in. bolts connecting the mill and the flanges served also as pivot points or hinge points.
At the front of the bagger, Weaver constructed a frame from angle iron reinforced with tube steel cross bars and triangular pieces of steel. This frame mounts to the top of the bagger gearbox and formed a base to mount the roller mill.
"I used two bolts with nuts on the top and bottom to connect the mill to the framework," says Weaver. "At that point the belt was slack and could be slipped on. To tighten the belt, I just screwed the bolt up to take out the slack."
The belt runs from a specially machined pulley on the gearbox to the main shaft on the mill. It is a high torque, flat belt only 3/16 in. thick, but able to handle about 200 hp.
"The belt works just perfect," says Weaver. "The machine runs real quiet."
The auger that feeds the mill has wheels, allowing it to pivot in place by the wagon as the mill/bagger moves forward. This allows the operator to set up the wagon ahead of the bagger and not move it again until the bagger has moved up ahead of the wagon.
Contact: FARM SHOW Followup, David Weaver, 2337 Welker Rd., Penn Yan, N.Y. 14527 (ph 315 536-2705).
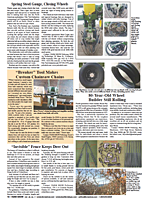
Click here to download page story appeared in.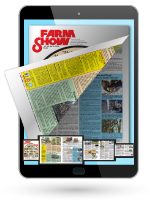
Click here to read entire issue
"Roller Mill Bagger" Does Two Jobs GRAIN HANDLING Miscellaneous 29-2-4 Running corn through a roller mill and then loading it into a bagger can be a great way to store feed, but doing it is a hassle. Because a bagger slowly moves ahead as the silage bag fills, the roller mill and the wagon emptying into it have to roll ahead as well.
"We had to have a tractor on the mill and one on the bagger," recalls David Weaver, who does custom bagging of shelled corn and silage as well as custom baling and manure application. "I figured that by putting a roller mill on top of the bagger, I would only need one tractor. It might not be any faster, but it would be a lot simpler."
Weaver began by ordering a custom-built roller mill from Isaac H Nolt, Leola, Penn. at a cost of about $8,500. It's designed to fit atop the bagger.
His plan was to adapt the 1,000-rpm roller mill to his 540-rpm bagger. It didn't work as well as he had hoped. So, he got Kelly Ryan Equipment Company to customize a bagger to run at 1,000 rpm's.
"The bagger came with a conveyor and a shield over the hopper," says Weaver. "I took the conveyor and shield off and adapted them so they could be reconnected again when needed for silage bagging."
He welded two flanges to a heavy crossbeam that runs across the rear of the bagger hopper. The 2 by 3-in. high pieces of 1/2-in. steel plate had holes drilled in them to match holes in the rear of the roller mill frame. Two 1/2-in. bolts connecting the mill and the flanges served also as pivot points or hinge points.
At the front of the bagger, Weaver constructed a frame from angle iron reinforced with tube steel cross bars and triangular pieces of steel. This frame mounts to the top of the bagger gearbox and formed a base to mount the roller mill.
"I used two bolts with nuts on the top and bottom to connect the mill to the framework," says Weaver. "At that point the belt was slack and could be slipped on. To tighten the belt, I just screwed the bolt up to take out the slack."
The belt runs from a specially machined pulley on the gearbox to the main shaft on the mill. It is a high torque, flat belt only 3/16 in. thick, but able to handle about 200 hp.
"The belt works just perfect," says Weaver. "The machine runs real quiet."
The auger that feeds the mill has wheels, allowing it to pivot in place by the wagon as the mill/bagger moves forward. This allows the operator to set up the wagon ahead of the bagger and not move it again until the bagger has moved up ahead of the wagon.
Contact: FARM SHOW Followup, David Weaver, 2337 Welker Rd., Penn Yan, N.Y. 14527 (ph 315 536-2705).
To read the rest of this story, download this issue below or click
here to register with your account number.