You have reached your limit of 3 free stories. A story preview is shown instead.
To view more stories
(If your subscription is current,
click here to Login or Register.)
Cement Mixer Converted To Self-Propelled TMR Mixer
Dairyman Dave Retzlaff needed a better way to produce Total Mixed Rations for his 50-cow herd. His solution was to build a self-propelled machine from parts off a combine and a cement mixer.
"It seems like everybody builds things out of combines, so I thought I would too," says Retzlaff.
One reason to go wi
..........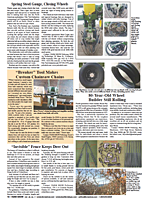
You must sign in, subscribe or renew to see the page.
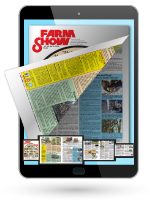
You must sign in, subscribe or renew to see the flip-book
Cement Mixer Converted To Self-Propelled TMR Mixer LIVESTOCK Feeding Equipment 29-2-18 Dairyman Dave Retzlaff needed a better way to produce Total Mixed Rations for his 50-cow herd. His solution was to build a self-propelled machine from parts off a combine and a cement mixer.
"It seems like everybody builds things out of combines, so I thought I would too," says Retzlaff.
One reason to go with a combine was the hydrostatic drive. Retzlaff wanted a mixer that could self-fill from the face of a silage pile and unload into feed bunks. Both tasks required the ability to creep ahead while keeping other systems under full power.
Retzlaff started out with a $2,000 New Holland TR70 from which he salvaged both axles, the 3208 Cat engine, cab, hydraulic system and electrical harness.
"I first built a main frame out of 4 by 6-in. steel tubing cross-braced with 5-in. sq. steel tubing," says Retzlaff. "I also reinforced the frame with 12-in. I-beams from behind the front axle and extending past the rear axle and part way under the engine mounts."
He mounted the combine drive axle on the rear end and mounted the engine at the rear as well. The drive axle is far enough forward that it carries most of the weight of the mixer mounted above it. The cement mixer was lifted intact from its original truck bed and set intact on the new framework, just ahead of the engine. The cab was mounted on the front right corner of the frame.
Retzlaff mounted a pto drive from a Uni-Harvester on the engine, giving him two drive shafts. He attached the cement mixer drive shaft to one and then ran a belt from the other shaft to the hydrostatic drive unit mounted on the axle. He also mounted a 32-gpm hydraulic pump under the engine. A four-band belt runs off the engine to the pump. A 3/4-in. valve directs flow to either the loader or the unloading auger as needed.
"It's a simple setup but I don't have reverse on either one," explains Retzlaff. "So far, I haven't needed it."
The hydraulic system from the combine provides power for steering as well as the header cylinders, which had been remounted on the loading elevator.
The loading elevator is housed inside a 12 by 12-in. square steel tube, fashioned from a gas station canopy leg. Retzlaff made the chain and flighting and had the pan the flighting runs over fabricated at a local metal shop. The top end of the elevator is hinged to two steel legs, which angle back from the main frame to the mouth of the cement mixer. When not in use, the elevator rests against the legs and the frame.
"One thing I would change is the size of the elevator," says Retzlaff. "With fluffy haylage it doesn't plug up, but the elevator flights can slide under. A wider elevator, say 20 in., would work with all kinds of feed and work faster."
Retzlaff designed and built a mechanical mouth to tear away silage at the face of silage bags and feed it into the elevator. This front unit is attached to the loading end of the elevator and pivots with the aide of a hydraulic cylinder. The pivoting action gives Retzlaff additional reach and control.
The facer itself consists of a bucket-shaped framework fitted with an auger and beater reel. Retzlaff welded flighting to a 4-in. steel pipe for the auger. It throws silage to the center and into the elevator. The beater reel is made from steel plate teeth welded on at 3-in. intervals. Each is staggered back from its neighbor by an inch. Retzlaff had a machine shop make stub shafts, which he welded to the pipe ends for mounting the beater and the auger.
The motor that drives the elevator chain also drives the auger and facer. While the elevator shaft turns at 1,000 rpm, the facer beater and auger turn slower. This helps ensure that they never overload the elevator.
To load the mixer, Retzlaff creeps up to the face of the silage bag and slowly raises the elevator against it. The beater tears away at the face, pulling material into the auger. Corn and soybean meal are simply augured directly into the mixer.
"The toughest part was building the front unit and matching the speeds of the facer, auger
To read the rest of this story, download this issue below or click
here to register with your account number.